Posting Rules | post new threads post replies post attachments edit your posts is are code is are are are | Similar Threads | Thread | Thread Starter | Forum | Replies | Last Post | | slongen | Construction, Maintenance & Refit | 0 | 05-05-2020 07:28 | | sona1111 | Construction, Maintenance & Refit | 22 | 29-07-2018 17:02 | | michaelmrc | Construction, Maintenance & Refit | 21 | 21-05-2009 13:17 | | mellenburg | Marinas | 4 | 29-09-2008 18:36 | Privacy Guaranteed - your email is never shared with anyone, opt out any time.  Boat Genesis is reader-supported. When you buy through our links, we may earn an affiliate commission at no cost to you. Learn more . 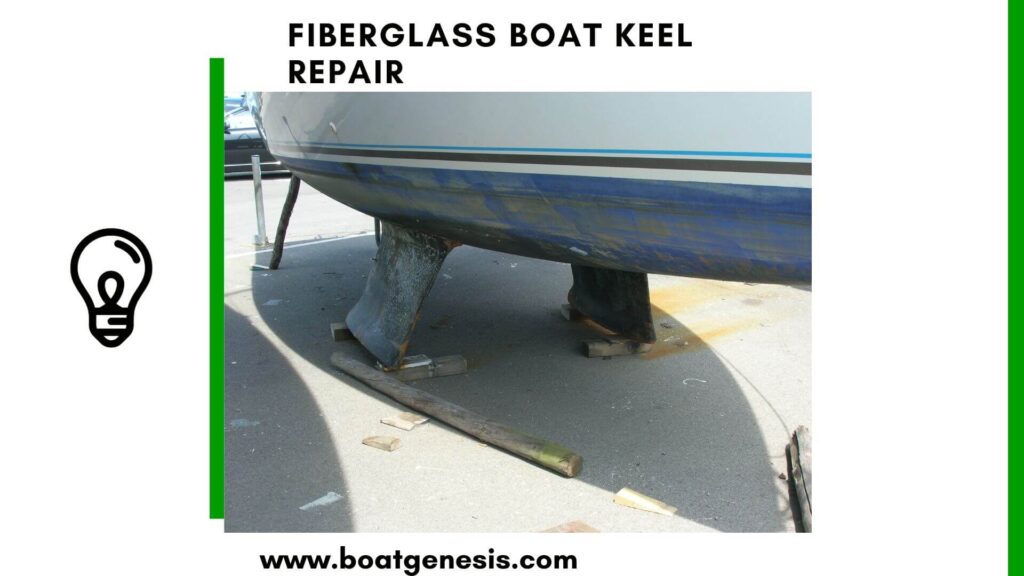 Fiberglass Boat Keel RepairHas your sailboat or powerboat sustained damage to its vulnerable keel? Impact with underwater objects can crack, chip or puncture a fiberglass boat’s keel, compromising structural integrity. When keel damage occurs, proper repairs are essential for restoring seaworthiness. This article provides a DIY overview of assessing damage and performing a fiberglass boat keel repair. 5. Fairing & Refinishing RepairsFiberglass boat keel repair guide, 1. inspecting keel damage. After a grounding or collision, thoroughly inspect the keel for cracks , fractures, holes and delamination. Look for stress cracks radiating from the point of impact. Check inside the boat along the keel joint for signs of damage. Determine how extensive the repairs need to be. Minor chip repairs may only require some basic grinding, filling and refinishing. Major cracks, holes and delaminated bottom skin necessitate more extensive fiberglass work. If damage compromises over 30% of the keel depth, professional repairs may be needed to meet safety standards. 2. Grinding Out Damaged AreasStart by sanding and grinding down all cracked, chipped and punctured areas with 36-80 grit disks to open up the damage. Remove loose fibers and degrade the gel coat surface to improve adhesion. Create a rough surface profile for the repair compounds to mechanically bond with. For cracks, the saw cut a V-groove along the length with a circular saw at least 1/8″ deep to increase the surface area. Grind damaged fibers at the root. Vacuum and solvent wipe repair areas to remove debris and grease before applying materials. 3. Filling Holes, Cracks and ChipsFill scratches, gouges , cracks and drill holes with thickened epoxy adhesive filler thickened with colloidal silica or micro balloons. Apply filler in layers until flush with the surface, allowing cure time between applications. For cracks, wet out the inside surfaces with neat epoxy before applying thickened epoxy. Overfill the repair and allow the adhesive to cure before final sanding. Finish filling holes and cracks by applying structured repair materials. 4. Applying Fiberglass Repair Laminates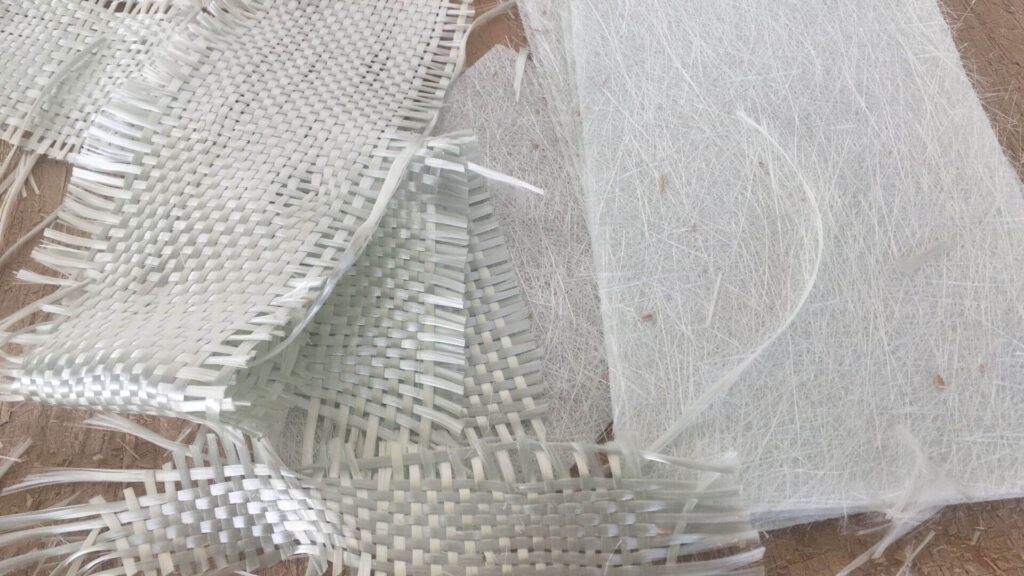 Cut several plies of woven fiberglass cloth to overlap damaged areas by at least 2″ on all sides. Pre-fill any cloth texture with epoxy filler. Wet out each layer of cloth with epoxy resin before applying it to the repair. Use a plastic spreader to smooth the cloth, removing air pockets and excess resin. Apply 4-6 layers of cloth based on existing laminate thickness. For cracked keels with bottom skin delamination, the detached skin may need re-bonding and supplementary layers of glass cloth overlap for added structural strength. Allow resin fill coats to fully cure between layers based on product guidelines. Once the repair plies fully cured, use 80-120 grit sandpaper to fair in the repair and blend with surrounding fiberglass. Fill any remaining pinholes or surface irregularities with polyester or epoxy filler/fairing compound, then sand flush. Solvent clean and apply three coats of two-part polyurethane topside paint to match your boat’s color. Lightly sand between paint coats. Touch up registration numbers, draft marks and antifouling bottom paint as needed. Final ThoughtsPerforming quality fiberglass repairs takes some work, but restored integrity and seamless refinishing is achievable with the right techniques. Follow safety precautions when grinding glass materials and mixing/applying resins. Use protective equipment and ensure adequate ventilation. With time, patience and the proper methods and materials, you can repair damage to your boat’s vulnerable keel without breaking the bank. Take things slow, allow adequate cure times and the result will pay off with a keel that’s shipshape. Your fiberglass sailboat or powerboat will be back cutting smoothly through the seas in no time! Share this post:Related posts, best gelcoat repair kit for boats in 2024. 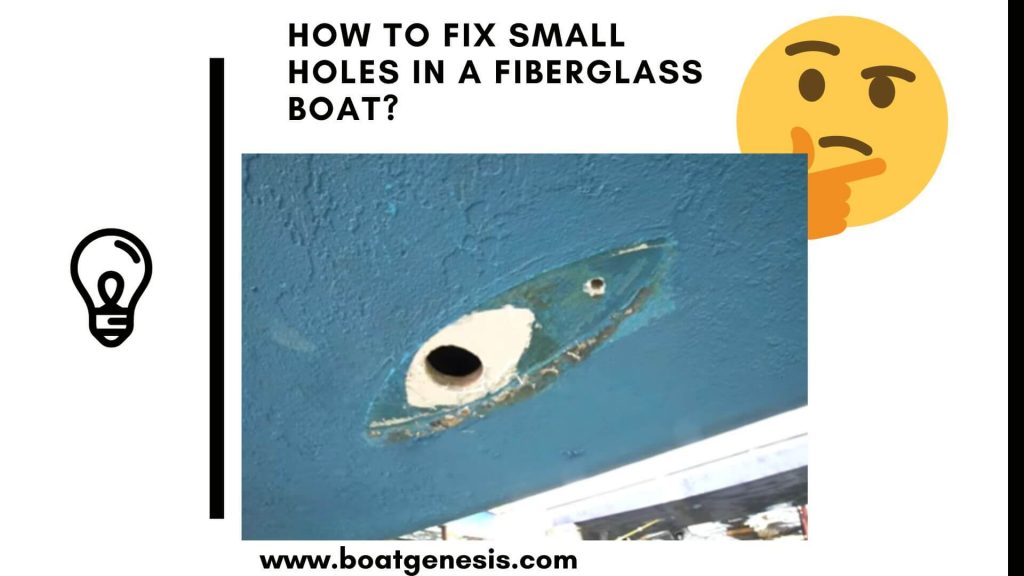 How To Fix Small Holes In A Fiberglass Boat? 6 Easy StepsRepairing a large hole in a fiberglass boat: definitive guide, leave a comment cancel reply. Your email address will not be published. Required fields are marked * Save my name, email, and website in this browser for the next time I comment. Boat Genesis is reader-supported. We try all the products we recommend - No freebies from manufacturers. If you click on our links, we may earn an affiliate commission, which helps support our website. Learn more . Subscribe To Boat Genesis Get updates on the latest posts and more from Boat Genesis straight to your inbox!  Keel maintenance and repair – Part 1by Simon Jollands | Boat Maintenance , Preparation , Yacht ownership  The job of a sailing boat’s keel is to control sideways movement through the water and to provide a counterweight to the sideways force of the wind on the sails, which causes a boat to heel over. Keels are designed to act as underwater foils that generate lift as the boat moves through the water, counteracting the leeward force of the wind and enabling the boat to sail closer to the wind. The most common type of keel used for sailing yachts is the bolted-on fin keel. Fin keels are usually made of cast iron, bolted through the undersides of GRP hulls with substantial stainless steel bolts. Other types of keel include bilge keels, shoal keels, encapsulated keels, lifting keels and canting keels, as used on racing yachts. While iron is the most common type of ballast, lead is also widely used. Cement or concrete is sometimes used in combination with scrap iron as ballast for wooden and steel boats, but this can lead to steel rusting from the inside and is not considered good practice. Some modern racing yachts have water ballast which can be pumped into tanks to help counterbalance heeling. Clearly, motor boats do not require deep keels to counterbalance the heeling effect and sideways force of a boat under sail, but nonetheless they do have keels designed to keep them stable and provide structural integrity. Displacement hulls are often ballasted to increase stability. As a result they have a low centre of gravity making them less susceptible to the wind and waves than planing hulls, which are designed for speed and performance. Keel problems It is very rare for a keel to fall off a boat. When this happens the incident often receives a lot of press attention as the subject is understandably of concern to boat owners, builders and designers. Marine accident investigators are usually called in and reports are published explaining the probable causes of these accidents. There are more common incidents involving keels that require inspections and repairs to be carried out.  Keel bolts inspection Keel bolts should be inspected once a year for signs of corrosion. Most keel bolts of modern boats with cast iron keels are studs, threaded into a tapped hole in the keel. Keel bolts can be made from either stainless steel or galvanised steel. Lead keels often have J shaped bronze bolts cast into the lead. Bronze is only used with lead keels as bronze and cast iron create a galvanic reaction. An inspection entails looking from the inside and outside of the boat: Outside check - If there is rust appearing along the hull to keel joint then this is a clear warning sign that the studs may be corroding.
- Look for any signs of movement between the hull and keel, such as splits in the seal or cracks in the hull area around the joint.
Inside check - Do a visual check of the fastenings in the bilges, making sure you take a look at all of them even if they are hard to access.
- Dry and clean the bilge – the bilges should be kept dry at all times to help prevent corrosion of the fastenings, even if they are stainless steel.
- Some staining and minor rust is quite common but heavier corrosion needs to be checked over carefully.
- Surveyors tap the studs with a hammer and know what sounds to listen for. A ringing sound is good, a dull sound is not good.
- Check for any stress cracks in the bilge area around the keel bolts, which indicate there has been movement. If you see damage like this then it would be wise to have the keel removed for further inspection.
Keel bolt corrosion Keel bolts can sometimes be withdrawn for inspection to check their condition and for any signs of corrosion. This entails first removing the nuts one by one and inspecting the threads for signs of crevice corrosion. Quite often, it is the middle part (the waist) of a bolt where the corrosion is taking place, which is where the hull joins the keel. This is caused by the failure of the seal at the hull-to-keel joint, which allows sea water to reach the bolts and corrode them. Under these circumstances, the seal will need to be replaced as well as any corroded keel bolts. If you have any cause for concern it is wise to ask an expert to take a look and advise whether the keel needs to be removed for further investigation and repair. Keel bolt and hull-to-keel seal replacement A typical repair involving keel bolt replacement and new hull-to-keel joint proceeds as follows: - A frame is prepared to support the keel when it is separated from the hull.
- The boat is supported in the boatyard hoist or crane.
- The keel bolt nuts and washers are removed from inside.
- The boat is hoisted a little off the cradle.
- As separation begins steel blades are inserted into the hull-to-keel joint crack to cut through the seal. Steel wedges may be hammered into the joint to encourage separation. This can take several minutes as seals are sometimes reluctant to give way.
- Once the hull and keel are separated the boat is lifted clear from the keel. The keel now rests in the wooden frame.
- The keel bolt studs are inspected. If any are badly corroded or distorted then they are removed and replaced.
- The old sealant is ground away from the flat surfaces of the hull join and keel top.
- The fibreglass hull around the join area is checked for stress cracks. If these are found then the hull will need to be strengthened with new layers of woven fibreglass mat and epoxy.
- The hull and keel top are prepared thoroughly for priming in order that the new sealant can be applied.
- The boat is slowly lowered back down onto the keel, then the backing plates, washers and nuts are fastened. Excess squeezed out sealant is wiped off.
- The nuts will need to be torque tightened according to the recommended keel bolt diameter torque settings as the seal beds down and checked again after the boat is relaunched for any signs of leakage.
 Navigating Through Rough Waters: Tips for Handling Adverse Weather Conditions in a Sailboat - Safe Skipper Boating & Safety Afloat Apps for phones & tablets www.safe-skipper.com Share on Facebook Share on Twitter Share on Linked In Share by Email  safe_skipper_apps Recent Posts- Navigating Through Rough Waters: Tips for Handling Adverse Weather Conditions in a Sailboat
- Docking a Motorboat
- Sailing Safely at Night – Best Practice
- Boating Etiquette: Do’s and Don’ts on the Water
- Navigating narrow channels
 Repairing Fiberglass On Boats (Complete Beginner’s Guide) Fiberglass boats are arguably the best kind of boats you can own. They’re lightweight, fun to use, and easy to maintain. They’re even easy to repair, and in this post on repairing fiberglass boats, we’ll tell you exactly how to do just that. Let’s get started! Table of Contents Fiberglass Basics You Should Know Fiberglass is a wonderful material that can be used to repair all sorts of things. Learn how to work with fiberglass, and you can repair boats, vehicles, bathtubs, and many other items. You can even learn to create your own parts, canoes, and even coolers. An entire lifetime could be spent learning how to build and repair things using fiberglass. But first, you need to know how fiberglass works as well as what it is. Fiberglass by itself is just a sheet of glass fibers woven or matted together. By itself, it is not hard, waterproof, or useful for anything. However, once you apply a chemical resin to the fiberglass, it becomes waterproof, hard, and incredibly durable. It also remains lightweight, which makes it great for applications such as aircraft, automobiles, and boating. The type of resin you use, the type of fiberglass you use, and the core material you use will determine just how hard and durable the constructed fiberglass becomes. Types of Fiberglass ClothThere are many different types of fiberglass cloths out on the market today. Some of these cloths include chopped strand mat, biaxial mat cloth, woven roving cloth, continuous roving cloth, carbon fiber cloths, and the list goes on and on. This being said, there are two types of fiberglass cloths that you’ll be working with: - Fiberglass fabrics, or cloths
- Fiberglass mat.
The fiberglass fabrics will be your main structural material, but you may end up using a fiberglass mat to help you work around turns and to help waterproof low-stress areas like the live wells. With these fabrics, you’ll also have different weights. These weights will help determine how thick and strong the material is. Popular boating fabric weights are 10 ounces, 6 ounces, 4 ounces, and 1.5-ounce cloths. These fabrics are sold by the yard and generally come in widths between three and five feet. The type of fiberglass fabric you choose will be determined by the application you’re using it for. Also, lighter cloths can be applied in multiple layers, so if you need more reinforcement, you can always combine a 4-ounce cloth and a 6-ounce cloth in two different layers to provide the thickness and strength of a similar 10-ounce cloth. Types of ResinThere are a lot of different resins out on the market these days, but the two you’ll most likely be working with are either epoxy resin or polyester resin. Epoxy resin is more expensive than polyester resin, but it is often considered stronger. It is also more versatile as the epoxy resin will bond well over polyester resin, but polyester resin may not work well over an epoxy. This being said, different epoxy materials will work better with different core materials. For example, the polyester resin will melt some foams and plastics. I found this out the hard way when I mixed some epoxy resin up in a plastic cup. The resin started leaking right through the bottom of the cup, and I was very thankful that I had decided to play with the fiberglass outside. Some other types of resin you might run into are polyurethane resin and silicone resin. These resins are even more expensive than epoxy resin, and it doesn’t really make sense to use them for boat repairs anyway. Core MaterialsThe core material is just the material that is encapsulated by the fiberglass cloth and resin. Core material on boats is usually balsam wood or a foam core. However, almost any material can become a core material. For example, I’ve applied several different types of fabric with polyester resin over the top of pieces of cardboard. The fiberglass and resin are so strong that it turns the cardboard into a hard shell that you can use to make many different things, including small boats. If you ever need to do a small one-off project that does not require structural support, think about using cardboard as a cheap and easy alternative to creating a mold or using traditional core material. This being said, your best bet is to use a core material that is meant for your particular application. For obvious reasons, being out on the water in a damaged balsa wood and fiberglass boat is a whole lot safer than being out there in a damaged cardboard boat. Also, keep in mind that you don’t always need a core material. Sometimes you can create a mold that simply holds the fiberglass and resin together until they dry and become components themselves. Many fiberglass hulls are built using molds that consist of a thick layer of fiberglass and resin, and they are designed to be very strong with many layers of built-up woven fabrics and mats with no core material. Camper shells are also built this way without any core material. If you’re curious about what this looks like, just do a quick search for fiberglass campers on this website, and you’ll see plenty of examples. When you’re doing repairs on an existing fiberglass boat, you may not be using any core material either. This is especially true if you’re just repairing a crack or hole in a non-load-bearing area. In this case, you’ll just be applying cloth over the crack and sealing it with resin. How Is The Fiberglass Applied?There are a few different ways that fiberglass can be applied. - Roll it on with a paint roller
- Paint it on with a brush
- Spray it on with a spray gun.
When doing fiberglass boat repairs, you’ll most likely be painting or rolling it on in small batches. The way you’ll do this is you’ll mix up a small amount of resin that you can successfully paint on over the fiberglass within about 15 to 20 minutes. This is about how much time you’ll have before the resin begins to dry and harden. If you mix too much resin, you’ll end up wasting it, so it’s important to start small until you get a feel for working with it. Also, keep in mind that all of your fiberglass should be laid out over the area you’re repairing before you begin mixing your resin. Once your resin becomes active, you won’t have time to go back and cut out pieces of fiberglass. General Tips for Working with Fiberglass As we alluded to earlier, fiberglass must be mixed before it can become active. This is usually done with a hardener. The manufacturer will tell you just how much hardener needs to be added to the resin. Gel coats can also be added to the resin, but this shouldn’t be done until you are on your final layer. If you apply the gel coat too early, you’ll end up having to sand the layer down before you can add any additional layers. Also, keep in mind that fiberglass resins are meant to be used at different ambient temperatures. If the temperatures are too high or too cold, the resin will not cure properly. You’ll know the resin didn’t cure correctly if the fiberglass feels tacky afterward. Safety Tips for Working with FiberglassFiberglass resins and hardeners can be toxic, and it’s important to keep them off of your body and out of your lungs. Personally, I only work with fiberglass outside, but any well-ventilated area will do. Also, if you’re working with polyester resin, you’ll want to wear a respirator. Not only is polyester resin toxic to breathe, but it smells awful. The smell is so bad that I won’t even leave the closed bottle of polyester resin inside my house for fear that it will make the house smell bad. You don’t want to get resin on your skin or your eyes either. Wear protective clothing, gloves, and safety glasses to prevent this from happening. For additional protection, you can also get a lotion that will work to coat your hands. This way, if the resin gets through your gloves, you’ll have an extra layer of protection between the resin and your skin. If the resin does end up getting on your skin, be sure to wash it off immediately. People have been known to develop allergies to epoxy resin, and once you get this allergy, you’ll never be able to be around epoxy resin again. Fiberglass Buying Tips- Always buy fiberglass by the roll. Unfortunately, many people will try to sell you folded pieces of fiberglass because it is cheaper and easier to pack, ship, and store it this way. Sadly, folding fiberglass cloth can weaken the strands, so when you buy fiberglass that is folded, you’re buying cloth that is already damaged.
- Buy the hardener with the resin. It’s always easier just to buy the hardener and gel coats with the resin. Different resins will need different amounts of hardener, and the manufacturer will usually sell the two as a kit.
- Get good mixing cups. A poorly mixed resin will not work properly. Get good mixing cups so that you can accurately mix the resin and get the most benefit from it.
- Buy it locally (at first). A local marine store owner can often offer you valuable tips for working with fiberglass, and they can help tell you where you went wrong when you run into trouble. You’ll probably end up paying a bit more for your resin, but you’ll often end up with some good and free advice.
- Buy the right fiberglass for the job. When you go to buy fiberglass, you’ll notice right away that chop strand mat is dramatically cheaper than all of the other types of fiberglass. There is a reason for this. Fiberglass mat is not very strong, and it can be difficult to work with. Only use fiberglass mat when the job specifically calls for it. Resins are expensive, so there isn’t any point applying them over inferior fiberglass cloths.
Repairing The HullBefore you decide to repair your own boat hull, you may want to do a reality check. Is the boat hull severely damaged? Is your boat an ocean vessel that is going to be put under a lot of stress? If you answered yes to these questions, you might want to save this project until you have a lot more experience with fiberglass repair. In this situation, a bad repair job could put your life in jeopardy, so the money you save will never be worth it. This being said, there are a lot of small hull repairs that you could tackle yourself without much risk. For example, a small hole in a small boat that you only take out on the lake shouldn’t be too much for you to handle. Small cracks or holes in the areas above the water line might not be a big deal either, but please use your best judgment. 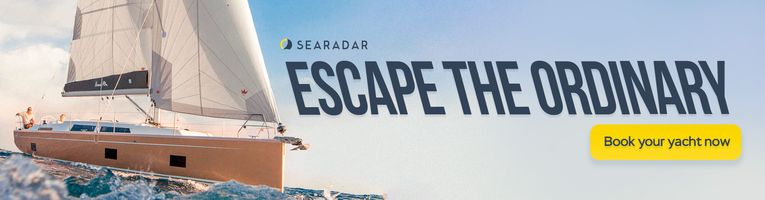 Repairing Holes in The HullTo repair a hole in the hull, you may need to get some new core material. Try to match the new core material with the existing core material. Make sure the remaining core material is dry. Once you have the core material, you’ll need to fit it into the hole. Next, measure and cut your fiberglass cloth. Lay the fiberglass over the area, using fiberglass tape if you have to. Once everything is in place, mix up your resin and apply it over the damaged area. You may need to do multiple layers. For professional repairs of ocean-going hulls, the surrounding fiberglass is ground back on a slope of 1:12 to make a large area to be repaired; a 1/2″ thick fiberglass structure would be ground back 6″ in every direction from the hole. The patch is then built-up with increasingly larger pieces of fiberglass mat and resin. Again, you need experience before trying this. Your final coat should be a gel coat that matches the color of your boat. Alternatively, you could repaint the boat after the repairs have been made. Repairing CracksBe careful when repairing cracks in your hull, as they could be a sign of bigger structural issues. For example, a balsa boat with cracks in it could have rotten wood inside the hull. However, if you just see some cracks from when you accidentally backed into a tree last week, feel free to try to take on the repairs yourself. You probably won’t need any new core material, but you will need some fiberglass and some resin to patch up the crack. Measure, cut, and layup your fiberglass before mixing your resin, and you shouldn’t have any trouble with the repair. One thought to keep in mind with a repair like this is that you’ll probably spend more time sanding and painting than you will be doing the actual repairs. The more time you spend sanding, the better the boat will look when you’re done. Repairing The Floor and DeckThe first thing you should do before making any repairs to the deck or the floors is to check to see how severe the damage is. Often-times, decks and floors are made from wood, and if they are spongy or have holes in them, the wood is probably rotten underneath. Before making any repairs to the fiberglass, you’ll need to take out this rotten wood and replace it. What seems like a small repair, in the beginning, can often end up being an extensive repair. If you don’t believe me, just look at all the free “project boats” listed on Craigslist. Oftentimes you’ll see that the person giving it away received the boat for free himself, thinking that he could do the repairs and get a free boat. Once he started to tear the boat apart, he realized just how much work and money would be needed and decided to give up on it. Once you do know what you’re in for, start replacing the decking and flooring, making sure to keep the materials dry until they are encapsulated with new fiberglass and resin. Also, be sure to make a note of where the different pieces of hardware are connected to the deck, as you’ll need to put them back on when your repairs are complete. If you’re careful, you can use the old decking that you pull off the boat as a template for creating your new decking. Once your new flooring is complete, secure it to the boat and begin placing the fiberglass cloth over it. Be sure to use a good amount of fiberglass as the decking will need to be strong enough to support people walking over it. Mix up your resin and apply it in small batches. If you have a large area to do, you’ll be tempted to make larger batches but don’t do this as you’ll only end up rushing the job or finding the resin sets up prematurely. Flooring AlternativesAnother thought to keep in mind is that you don’t always need to replace your wood flooring with wood. Some people will skip the fiberglass altogether and simply install an aluminum floor instead. This can be useful in certain applications but not very useful in others, so you’ll need to analyze your particular situation before you decide to make any changes. If you do decide to skip the fiberglass, just be careful to find out what changes this will have on the weight of your boat. Making a heavier boat could reduce your boat’s max capacity and affect the way your boat sits in the water. Repairing The KeelThe keel is an integral part of a boat. On a sailboat, the keel keeps the boat upright in the water and helps to keep it stable in heavy winds. Being at the bottom of the boat leaves it much more vulnerable to scraping the ground and running into rocks. For this reason, a keel can often take damage even when the rest of the boat remains trouble-free. The question is, do you want to repair this damage to the keel yourself? If you have a small recreational boat that you can easily bring up on land, I’d say go for it. You can flip the boat over in your backyard and spend as much time as you need applying a new resin and gel coat to the keel. For boats that you know will be scraping the bottom again, you may want to apply a keel guard as well. This will help protect your keel, so you don’t have to constantly make repairs each season. Repairing The TransomA solid transom will ensure that your boat’s engine doesn’t fall into the water. If you’re going to make this repair yourself, make sure you’re prepared to do it properly. Oftentimes the core of the transom needs to be replaced, and you’ll want to make sure you replace it with a material that is as strong or even stronger than the original. This is especially true if you’ve upgraded the original boat engine to something bigger and heavier. Once you’ve replaced the core material, the steps for making the repair remain the same. Apply your fiberglass boat cloth and use as many coats of resin as you need to get the job done. This repair includes a lot of hard edges, so you may need to overlap your layers of fiberglass at the top to get a good seal. Take your time and make sure the fiberglass wraps properly, or you’ll end up having to do a lot of sanding at the end of the job. Also, be careful to account for where the engine will be mounted so that you can match the hardware appropriately. Repairing HatchesHatches are easy repairs, and they’re great for getting started with fiberglass. When replacing a hatch, use the existing hatch to make a template for the new one. The new hatch should be easy to make, and you won’t have to use a lot of thick fiberglass cloth since it won’t be the main structure of the boat. The main thing to keep in mind when doing this repair is that the hatch will need to be sealed properly afterward. Oftentimes, people will do a great job repairing or replacing the fiberglass hatch, but they won’t seal it properly afterward, and they end with a leaky hatch. Repairing ScratchesScratches in the fiberglass usually don’t require extensive repairs, and the cost is usually minimal. The reason for this is that the fiberglass does not need to be replaced, and the core material is not yet affected. Unfortunately, some deep scratches in the gel coat can end up creating a lot of prep work. You’ll end up needing to do a lot of sanding to get the boat to look new again. You’ll also need to do a good job matching the color. If your boat is new, this may not be a problem, but if your boat has been out in the sun for a while, you won’t be able to use the original boat color as it will end up being too dark. You’ll have to color match the boat, or you’ll have to resign yourself to painting the entire boat over again. DIY Costs vs. Professional CostsDoing repairs yourself will usually save you money, and they can sometimes even save you on time. However, some jobs are too big to be done by beginners, and some jobs just take too much time for the DIY repair to be worth it. I’ll try to give you a breakdown of some of the costs here so you can decide for yourself whether or not the repair is worth paying for or doing yourself. Example costs from FiberGlassSite.com:- 6-ounce fiberglass cloth 50” wide and 5 yards long. – $25.00
- 1 gallon of polyester resin with hardener. – $39.00
With this much cloth and resin, you could do a lot of small repairs of cracks and holes. A simple hole or crack repair might cost you $50.00 each, so you’d definitely save money on smaller repairs, and you may even have some extra fiberglass left over for the future. For a balsa core deck repair, you might want ¾ inch core. This costs about $50.00 for a 2’x4’ piece. You’ll also need a 10-ounce fiberglass cloth and polyester resin. This repair might end up costing you a couple of hundred dollars, but it could save you a thousand. Foam core used for repairing heavy damage to the hull of a sea-going vessel will need to be very strong. Not only this, but you’ll need to consult with a marine technician to determine what the best combination of foam, resin, and fiberglass should look like. Between material costs and consulting costs, you’ll end up spending thousands of dollars. You’ll also end up spending a lot of time, and you may devalue the worth of the boat since a buyer might not feel safe buying a boat that was repaired by an amateur. In this case, you may be better off paying a professional boat repair company to do your repairs. Final ThoughtsWorking with fiberglass can be tricky, but it can also be a lot of fun. Learn how to work with fiberglass, and you’ll find an almost endless number of projects to take on. Just keep in mind that working with fiberglass is not cheap or easy to get into. If you decide to take on fiberglass projects, be prepared to spend some time and money doing so. Also, be prepared to mess up a few projects while you’re learning. Click to share...  - Forums New posts Unanswered threads Register Top Posts Email
- What's new New posts New Posts (legacy) Latest activity New media
- Media New media New comments
- Boat Info Downloads Weekly Quiz Topic FAQ 10000boatnames.com
- Classifieds Sell Your Boat Used Gear for Sale
- Parts General Marine Parts Hunter Beneteau Catalina MacGregor Oday
- Help Terms of Use Monday Mail Subscribe Monday Mail Unsubscribe
Cast Iron Keel Repair- Thread starter docschreiber
- Start date Jun 9, 2015
- Forums for All Owners
- Ask All Sailors
docschreiberI have a '72 Coronado 23-2 that I recently purchased. My intention was to buy a "ready-to-sail" boat, but due to various circumstances that did not happen. I am a complete newbie to sailing and boat repair. The keel (Iron, I think....) had multiple areas of rust showing, so I stripped it down to metal with an angle grinder and 80 grit sanding pad. On the starboard side I have found a large area (1 foot wide by 10 inches tall by ~5-7mm deep) area that someone had filled with Bondo and painted over. I have cleaned it out, and am searching for the best way to fix it right. Any help is greatly appreciated! I've tried uploading pictures here, but keep getting upload errors on the photos. I've reviewed the guidelines and the pics should load, so if anyone can help here I'll get photos up. I put them on my facebook page and made them public, so anyone can view them there. Sorry for the extra step. https://www.facebook.com/chris.schreiber.182  My last boat had a cast iron keel in similar condition. As I recall, I stripped it to bare metal, treated it with a product called "ospho" sealed it with epoxie, faired it with epoxie with thickener (don't remember what I thickened it with) put on a couple of more coats of epoxie and bottom paint. Still looked good when I sold the years later. Good luck and welcome to the wonderful world of sailing.  Phil HerringSorry about that, the photos were my fault. I was changing some server settings and caused the problem. Should be working now.  did those settings have anything to do with the gear adds.....when i click on something for sale i get a blank page and have been for 2 days now  Quite a project to start with! Wow! Starting with a cast iron keel, you've tackled a big one right away, but you're on the right track! Hopefully, you'll get input from a couple of others who've done the same job. One important item in the restoration process is to make sure that you seal it (the 'ospho' step?) right away when you get to bare metal. Don't let it set for a long time between reaching bare/clean metal and sealing it. Especially with the humidity in TN. I let the folks in the boatyard tackle my cast iron keel (pretty much a necessity with our rules on collection and disposal of materials), and I was glad that I did! They had to use a needle gun to remove the old paint and rust, then barrier coated with two coats of epoxy and then bottom paint.  You can fill and fair that keel with West System 610 thickened epoxy; however, that is expensive. You can make your own with West System epoxy resin, slow hardener, and West 404 High Density Filler. The 404 is for underwater use. Mix the resin and filler, adding filler til you have a thick paste, a little thicker than you want. Then add the right amount of harder and mix that in. Then fill and fair the damage / voids in the keel. Mix it in a wide Tupperware container to make it easier to mix and to keep it from kicking. I would use a thinner mix on the rest of the keel to make it easier to spread and get an even coat. Use the West System pumps to get an exact ratio. After the epoxy residue hardens in the pan, just flex the pan a little to break it out. Thanks, Andrew Cast iron can be welded as well. Maybe one of our welders will come on and explain the process as I am at least aware that it is a precise concept to get it right. Preheat the cast iron? Chief actually chief it can be welded ......but it is a bear to do..... yes preheating is one thing that has to be done and after welding it ...it may have to be cooled down slow and controlled as in cooling it down in temp drops ...most of them are made of very low grade materials or have a lot of surface rust scale in some cases it may be better to have a new one made from a casting company...there are a lot variables in this process...but from his description i would not worry about welding it just fill it with a good grade epoxy filler and fair it out and go on Woody: I figured you might address the welding prospect. Thanks for giving us more detail on that. Chief  Agprice and Sprega called it, Strip to bare metal Treat surface Barrier coat Epoxy fill Barrier coat Paint Welding would be a disaster even if you could figure out a way to do it. You want SMOOTH surface. The Ospor step chemically changes any surface rust to an inert substance, ready to be barrier coated. So no rush. Jackdaw said: Agprice and Sprega called it, Strip to bare metal Treat surface Barrier coat Epoxy fill Barrier coat Paint Welding would be a disaster even if you could figure out a way to do it. You want SMOOTH surface. The Ospor step chemically changes any surface rust to an inert substance, ready to be barrier coated. So no rush. Click to expand I wasn't suggesting welding. I was just curious as to viability and sailing safety and if welding would be better in this case. I got the answer from you two and that was my objective; for clarification for all of us. Thanks, Chief  I pulled the keel and ground the rust off. I the wire wheeled it. The next step or actually three steps was the POR15 process. Degrease and then etch with the recommended products. Got everything from Eastwood. I then top coated the whole thing with Rustoleum industrial gray. Worked mint. Second time BTW. First time was all the prep work and a rust converter before Rustoleum primer and paint. POR is bulletproof. Touch up where you hit rocks. Yes the Ocean is shallow. Who knew!! Happy Sailing!! Ken B CMDRE North East Trailer Sailors Jackdaw is right about the ospho. Also, I have had EXCELLENT results with epoxie from US Composites. Way cheaper than west.  Sprega said: Jackdaw is right about the ospho. Also, I have had EXCELLENT results with epoxie from US Composites. Way cheaper than west. Click to expand - This site uses cookies to help personalise content, tailor your experience and to keep you logged in if you register. By continuing to use this site, you are consenting to our use of cookies. Accept Learn more…
- New Sailboats
- Sailboats 21-30ft
- Sailboats 31-35ft
- Sailboats 36-40ft
- Sailboats Over 40ft
- Sailboats Under 21feet
- used_sailboats
- Apps and Computer Programs
- Communications
- Fishfinders
- Handheld Electronics
- Plotters MFDS Rradar
- Wind, Speed & Depth Instruments
- Anchoring Mooring
- Running Rigging
- Sails Canvas
- Standing Rigging
- Diesel Engines
- Off Grid Energy
- Cleaning Waxing
- DIY Projects
- Repair, Tools & Materials
- Spare Parts
- Tools & Gadgets
- Cabin Comfort
- Ventilation
- Footwear Apparel
- Foul Weather Gear
- Mailport & PS Advisor
- Inside Practical Sailor Blog
- Activate My Web Access
- Reset Password
- Customer Service
  Blue Jacket 40 Used Boat Review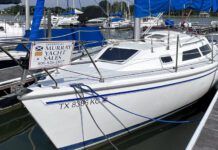 Catalina 270 vs. The Beneteau First 265 Used Boat Match-Up Ericson 41 Used Boat Review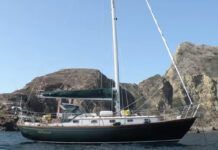 Mason 33 Used Boat Review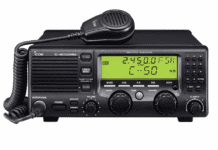 How to Create a Bullet-Proof VHF/SSB Backup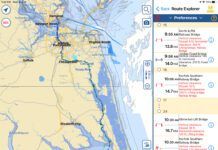 Tips From A First “Sail” on the ICW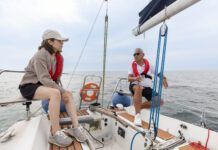 Tillerpilot Tips and Safety Cautions Best Crimpers and Strippers for Fixing Marine Electrical Connectors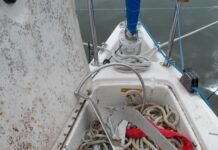 Polyester vs. Nylon Rode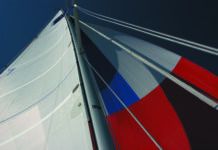 Getting the Most Out of Older Sails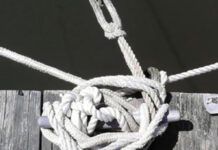 How (Not) to Tie Your Boat to a Dock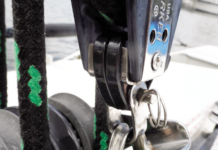 Stopping Mainsheet Twist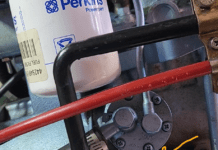 Fuel Lift Pump: Easy DIY Diesel Fuel System Diagnostic and Repair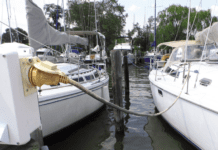 Ensuring Safe Shorepower Sinking? Check Your Stuffing Box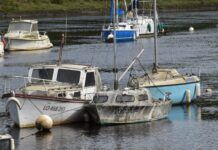 What Do You Do With Old Fiberglass Boats?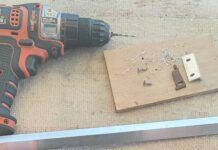 Boat Repairs for the Technically Illiterate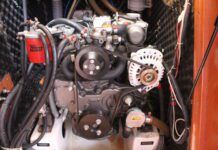 Boat Maintenance for the Technically Illiterate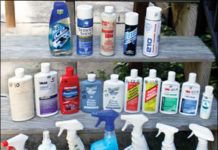 Whats the Best Way to Restore Clear Plastic Windows?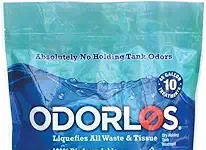 Stopping Holding-tank Odors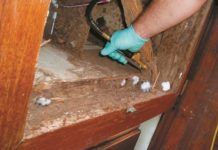 Giving Bugs the Big Goodbye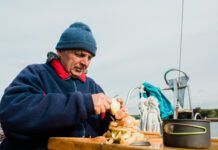 Galley Gadgets for the Cruising Sailor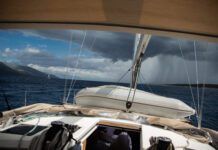 The Rain Catcher’s Guide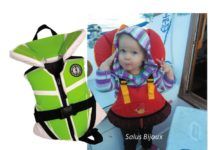 Sailing Gear for Kids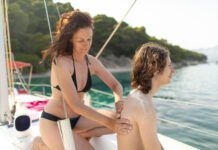 What’s the Best Sunscreen?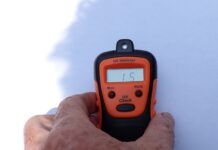 UV Clothing: Is It Worth the Hype? Preparing Yourself for Solo Sailing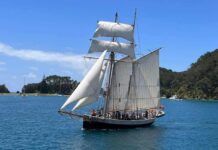 R. Tucker Thompson Tall Ship Youth Voyage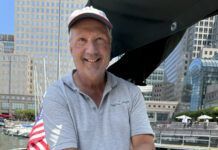 On Watch: This 60-Year-Old Hinckley Pilot 35 is Also a Working…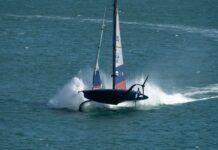 On Watch: America’s Cup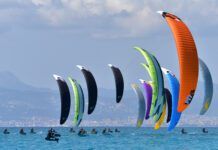 On Watch: All Eyes on Europe Sail Racing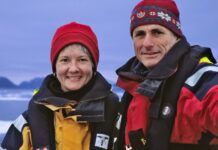 Dear Readers- Boat Maintenance
- Sails, Rigging & Deck Gear
Checking and Replacing: Keelbolts, Part 1 It is almost impossible to generalize about the longevity of keelbolts, since so many variables influence the life of a metal immersed in water.Nevertheless, this safety margin does not guarantee eternal life for keelbolts. Corrosion takes its toll, sometimes more quickly than you might think. It is almost impossible to generalize about the longevity of keelbolts, since so many variables influence the life of a metal immersed in water. If there are signs of deterioration in underwater fittings such as sea-cocks, struts, or propellers, the same forces may be chewing away at the bolts which secure the ballast that keeps your boat rightside up. Checking and Replacing Keelbolts How can you be sure about the condition of your keelbolts? Simple. You look at them. This does not mean looking at the nuts in the bilge. This means pulling one out and examining it from top to bottom. In practice, this may be a monumental task, or a simple chore Keelbolts are commonly installed in one of three ways. They can consist of long rods, threaded at either end, which extend from the bilge of the boat all the way through the ballast casting, with nuts set up in recesses in the bottom of the casting. This arrangement is usually seen in boats with fairly long, shallow ballast castings, rather than fin keels. It is used with both iron and lead keels. Sometimes, rather than bore all the way through the casting, pockets are cast or cut near the top of the ballast casting. The holes for the bolts are drilled from the top of the casting into the pocket, and large nuts and washers installed. The pockets are then filled with lead or cement. The advantage of this arrangement is that shorter bolts can be used, and the labor of drilling entirely through a deep ballast casting is avoided. This method is seen on lead keels, and can be used on deep fins as well as shallow castings. It is rarely used with iron keels. Tapping into the top of the casting, then screwing a threaded rod into place, is another common technique. This can be done with either iron or lead, although it is more commonly seen in iron keels. It is not necessary to tap very far into the top of the keel. As a rule, if the bolt is threaded four times the nominal bolt diameter into the top of the keel, it will hold the full strength of the bolt. In practice, it is probably best to drill and tap to a depth of five or six diameters, since it may be difficult to get really good threads in the very bottom portion of the holes, and debris may keep the bolt from reaching the bottom of the hole. Another technique used with fin keels is to cast the bolts in place when the keel is cast. This can only be done with lead keels. If you tried to do it with cast iron, you would melt the bolts. Cast-in-place keelbolts should be fitted with nuts and washers inside the keel mold before the casting is made. It is folly to assume that the molten lead will neatly flow into the threads of each bolt, just as if the holes had been tapped in after the casting was completed. A cast thread has less holding power than a cut thread, and the shrinkage of the casting as it cools may yield a very poor fit between the threads of the bolt and the lead of the keel. Sometimes, the keelbolts will be bent at an angle inside the mold before the keel is cast, the theory being that it would be necessary for the bolts to straighten out before the keel could pull loose from the boat. The disadvantage of this method is that it makes it almost impossible to remove the bolts from the lead for examination or replacement. Unfortunately, this is one of the most common ways of installing bolts in a modern fin keel. It may not be clear from looking at your keel exactly how the bolts are installed, except when the bolts go all the way through the casting, or when pockets in the casting are used. Grinding the keel to bright metal almost always shows up pockets in either the bottom or side ofa keel attached using either of these methods. The construction plan for your boat probably shows the way the designer intended for the bolts to be installed, but it is fairly common for builders or keelmakers to modify the designer’s plans to the way they normally do the installation. If the builder of your boat was not the molder of the keel, he may have no idea how the bolts are installed. The builder’s primary concern is that the bolts protrude from the ballast casting in the proper locations, so that the keel may be bolted to the hull with minimum difficulty. Removing Keelbolts In some areas, portable x-ray facilities may be available, making it possible to examine bolts in place without going through the trouble of removing them. This method works for steel and stainless, but is almost useless for bronze, since the corrosion process is somewhat different. More often that not, however, removing a keelbolt for examination is the most practical way to determine its condition. This can be a simple job, or it can be almost impossible. While it isdifficult to generalizeabout which type of keelbolt installation makes for the easiest extraction, theoretically at least, a stud threaded into the top of the casting should be the easiest to remove. A knowledgeable boatbuilder will not cut the tops of the keelbolts off flush with the tops of the nuts. Instead, he will leave enough threaded rod projecting through the nut so that a second nut can be tightened down onto the regular keelbolt nut to lock it in place, preventing the nut from turning on the rod when you try to unscrew the rod from the keel. Here’s the method. First, using a socket wrench, an extension, a breaker bar, and a liberal dose of penetrating oil, loosen the keelbolt nut slightly on its rod. If you are lucky, the whole rod will start to turn out, instead of the nut merely loosening on the rod, and you can extract the bolt in one simple operation. Of course, if the rod starts to turn freely, you may also have sheared the bolt, but if it broke that easily, it needed to be replaced anyway. If the nut has loosened on the rod, back if off just enough to clear the washer or backing plate on the inside of the hull. This means that when you apply torque to the nut to try to back the stud out, you won’t have to overcome the friction of the nut against the washer before torque is applied to the bolt itself. If nothing wants to turn, stop for a moment. Three things can happen if you apply enough torque: either the nut will turn, the stud will turn where it is threaded into the casting, or the rod will shear. What are you going to do in each case? If the bolt shears, you will have to drill through the hull into the ballast casting, tap a new hole, and install a new bolt in a slightly different location from the original. Is there room to do this? Will you have to install some reinforcement in the hull to carry the load of the new bolt? If you can’t answer these questions in a reasonable way, you should not try to remove the bolts. If the nut has loosened and there is enough thread sticking out, take another nut of the same size and thread it down firmly on the keelbolt nut. Hold the lower nut in place while tightening the upper nut. You will really have to crank these together to get them to hold in place. Usually, the nuts used on keelbolts will be of the configuration called “full heavy” nuts. For the jamming nut used on top, a “full finished” or “finished jam” nut should be used, if possible. These nuts are slightly smaller than “full heavy” nuts. In practice, this means that you can slip a socket over the two nuts to loosen them, and if the nuts are properly aligned, all the torque of the socket will be transmitted to the lower nut, and there will be little tendency for the upper nut to loosen. With the two nuts jammed on the bolt, it should be possible to turn the bolt out, once again using a socket, an extension, and a solid breaker bar. With very large bolts it may be necessary to use a pipe extender over the solid breaker bar to get adequate leverage. Use a little common sense with breaker bars and extensions, because you can get tremendous leverage on the nuts and bolts using them. Mild steel bolts in a cast iron keel may seize solidly. Bronze or stainless bolts in lead should break free quite easily. Bolts which consist of long rods passing entirely through the ballast casting can usually be driven out from above. The holes in the bottom of the keel are usually plugged with concrete, wood, or some type of hard putty. The first step is to loosen the nut at the top of the bolt. Unlike the situation with a bolt tapped into the keel, you must be able to loosen the nut at the top of the bolt. It is best to apply penetrating oil, and even heat from a propane torch, to free these nuts before applying a lot of torque. Heat is extremely effective in loosening seized nuts, but it must be applied carefully to avoid damage to a fiberglass or wooden hull. Traditionally, asbestos cloth is used around something you are heating up to avoid damaging adjacent surfaces, but asbestos is a material that must be used with extreme caution, since it is a known health hazard. Loosen the nut until it is flush with the top of the bolt in the bilge. Then strike the nut squarely with a heavy hammer. A light hammer will do little more than peen over the end of the bolt, causing you a lot of trouble. Needless to say, the confines of the bilge of your boat are pretty close for wielding a sledge hammer, but that is exactly what you will have to do. If the bolts are deep in the bilge, you may have to rest a rod on top of the nut, and strike the rod rather than the nut. You will need a helper wearing heavy gloves to gripthe rod, which will have to be held rock steady. Obviously, the helper is going to have to have a lot of faith in your ability to strike the rod, rather than his or her hands. A couple of heavy blows should free the bolt, and the nut will be driven down to the backing plate again. If you did not back the nut up flush with the top of the bolt, there is a good chance you have succeeded inpeening the top of the bolt, so that the nut cannot be backed off. A few minutes with a grinder or file should relieve the upset head of the bolt. Check the bottom of the keel. Have the plugs fallen out, and is the nut moving out of the keel? If the nut has not budged at the bottom of the keel, but has moved an inch lower at the top, there is a good chance that the bolt is crumbling under the blows of the hammer, an indication that replacement is long overdue. It should be pretty obvious that the boat can not be resting on its keel on the ground to this job. The keel must be blocked up, and the supports must be clear of the part of the keel through which the bolts pass. With a deep keel, it may also be necessary to dig a hole under the keel to get enough depth to drive the bolt free. It is possible that the keelbolts could be several feet long, necessitating extremely deep holes under the keel in order to remove them in one piece. An alternative, when you know you are going to replace the bolts anyway, is to drive the bolt out as far as you can, cut it off, then drive and cut again. Once the bolt has started moving, it should require relatively little force to finish driving it out. When the bolt is driven down flush to the inside of the hull, a driving rod will have to be used to finish the job. This should be a long piece of round bar stock that is both smaller in diameter and softer than the keelbolt; smaller in diameter so it won’t jam in the hole, and softer so it won’t damage the top of the bolt as it is being driven. Old bronze prop shaft-every boatyard has tons of this lying around-is ideal for the job. Keelbolts which do not extend through the keel, but instead have nuts installed in pockets in the casting near its top, are likely to be the hardest to remove, since they can not be driven out. Instead, you will have to locate the pockets by grinding off the paint on the outside of the keel. If they are plugged with wood or putty, cut it out with a chisel. If they are plugged withlead, you will have to melt the lead out with an acetylene torch, which can be rented for the occasion. Once the plugs are removed, take the nuts off the bottom of the bolts in the pockets. Now comes the tricky part. If you are lucky, you might be able to turn the bolts out, just like studs threaded into the top of the casting, using a combination of turning and pulling at the same time. It helps if someone else pries up on the bottom of the bolt from the outside at the same time. Usually, if you can get the bolt to turn, you will be able to pry it out. The alternative is to jack the bolt out from inside the boat. Remove the keelbolt nut on the inside of the boat, and replace the existing backing plate or washer with a heavy steel plate, through which you have drilled a hole the diameter of the bolt. A pair of hydraulic or mechanical jacks is then used to pry the bolt upwards. Some ingenuity in fabricating the jacking plate may be required to make it possible to get the jacks under the plate. Don’t try to pull the bolt out using a come-along attached to a deck beam or the cabin overhead unless you are willing to take the risk of looking very foolish when the deck collapses into the bilge. If your keelbolts were installed by casting the bolts in place with nuts and washers, you may be able to back them out, just like studs tapped into the keel. If bent rods were used in place of nuts and washers, you may be out of luck. Instead of replacing keelbolts, you will have to add more bolts when the time comes. In Part II, in the next issue, we’ll look at procedures for testing keelbolts, the options in metals for keelbolts, plus a few thoughts on replacing bolts found to have outlived their useful life. RELATED ARTICLES MORE FROM AUTHORLeave a reply cancel reply. Log in to leave a comment Latest Videos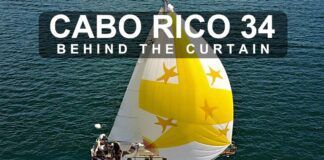 Cabo Rico 34 Boat Review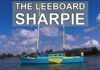 Super Shallow Draft Sailboat: The Leeboard Sharpie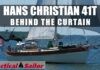 Hans Christian 41T – Boat Review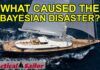 Seven dead after superyacht sinks off Sicily. Was the crew at...Latest sailboat review. 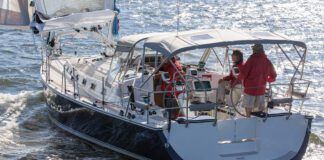 - Privacy Policy
- Do Not Sell My Personal Information
- Online Account Activation
- Privacy Manager
 Religious corporation, boat repair included in 29 new businesses in Central NY- Updated: Sep. 10, 2024, 8:02 a.m.
- | Published: Sep. 10, 2024, 8:00 a.m.
- Sharon Dellinger | [email protected]
County Clerk offices in Onondaga, Cayuga and Madison counties registered 29 new businesses during the week of Sept. 3 through 6. No businesses were registered on Sept. 2 due to the Labor Day holiday. The new businesses included a ministry and a boat repair service. One business closed in Cayuga County and reopened under new ownership. If you purchase a product or register for an account through a link on our site, we may receive compensation. By using this site, you consent to our User Agreement and agree that your clicks, interactions, and personal information may be collected, recorded, and/or stored by us and social media and other third-party partners in accordance with our Privacy Policy. 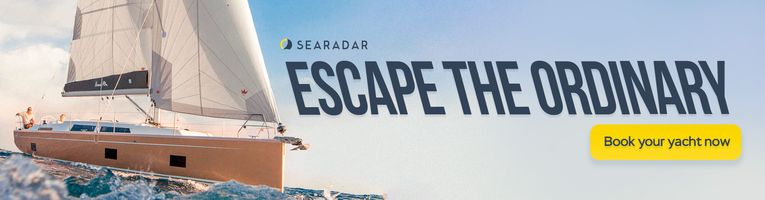 |
COMMENTS
Re: How to fix or repair a keel that has exposed or pitted fiberglass repair with a kevlar reinforced epoxy paste - you can use glass with it , but sounds like you don't need to google wet dry 700 epoxy Paul Oman - MS. MBA A.K.A. "Professor E. Poxy" Internet Epoxy Confederation (IEC) Homepage epoxies since 1994
The. purpose of this inspection is to identify and report to the Owner the condition of the keel and keel structure observed during this inspection. It is the responsibility of the Owner to undertake any repairs. Consult the Owners' Manual for the specific boat, steering system and type of keel (e.g. fin, lifting, swinging, full length).
Ship Wright Chris Carl shares his step by step process for fiberglass keel repair.
To make sure your keel doesn't begin to corrode again, you must completely isolate the surface of the keel from the bottom paint with an epoxy barrier. This is a two-stage process. First, the keel must be primed with a vinyl primer, such as Regatta Vinyltex 50/51 or Interlux Viny-Lux Primewash 353.
Repairing that keel is hard work. Take the advice of gloves but use eye and dust mask or better yet a respirator. When compeltly sanded, take a break and wash off the keel. In additon, wash off the top of the boat so the dust will not settle in the fine pores of the gel coat on top of the boat; otherwise it is heck to get off.
To hold the goop in place, screw in a couple of screws into the damaged area, this will hold the goop in place while curing. Re: Hit a rock. Minor Keel damage. How to repair. I hit a rock last year in my new (used) Hanse 470.
If the keel is truly in distress, loss, (once the keel is stabilized in a brace, the nuts removed and the boat lifted) the keel will drop right down with little effort and the inspection and a repair process can start. Otherwise, the removal work could take a day or more and a lot of blood sweat and tears. ... Contact us today for your keel ...
Fiberglass Boat Keel Repair Guide. 1. Inspecting Keel Damage. After a grounding or collision, thoroughly inspect the keel for cracks, fractures, holes and delamination. Look for stress cracks radiating from the point of impact. Check inside the boat along the keel joint for signs of damage. Determine how extensive the repairs need to be.
Keel Bolt Repair Options. In a few of our past reports on boat financing, Practical Sailor discussed how to pre-inspect your potential dreamboat before committing to the next step and how to bring in a surveyor. Although the articles are geared to the prospective buyer, it is just as relevant to the owner of an older boat.
Keel bolt and hull-to-keel seal replacement. A typical repair involving keel bolt replacement and new hull-to-keel joint proceeds as follows: A frame is prepared to support the keel when it is separated from the hull. The boat is supported in the boatyard hoist or crane. The keel bolt nuts and washers are removed from inside. The boat is ...
Fixed Keel Repair and Maintenance . ... Check when boat is on the hard with around 70% of weight on keel. Keel Stub Wood Removal. Keel Bolt Leak Repair. Keel Crack Repair. Mast Compression Post Block Repair . Catalina Direct is the largest supplier of Catalina Yacht parts in the country. We specialize in parts, custom up-grades, and accessories.
Used Boat Buying: Keel Repair and Hull Fairing. Paul Grimes. October 21, 2010. NEWS AND EVENTS. Throwback Thursday: Australia II's Winged Keel Design. Gary Reich. March 27, 2014. Boat Reviews. Southerly 45, Next Swing-Keel Cruiser in Build. John Burnham. January 27, 2011. Boating Guides. Boat Buyer's Guide.
The keel is an integral part of a boat. On a sailboat, the keel keeps the boat upright in the water and helps to keep it stable in heavy winds. Being at the bottom of the boat leaves it much more vulnerable to scraping the ground and running into rocks. For this reason, a keel can often take damage even when the rest of the boat remains trouble ...
The boat is in very good condition; however, when I pulled it out of the water at the end of the season in early October this year I noticed a slight crack in the keel that extends around the entire keel, about one third down from the hull. A friend looked at this condition and called it the "Catalina Smile," explaining the crack occurs on ...
I have a '72 Coronado 23-2 that I recently purchased. My intention was to buy a "ready-to-sail" boat, but due to various circumstances that did not happen. I am a complete newbie to sailing and boat repair. The keel (Iron, I think....) had multiple areas of rust showing, so I stripped it down to metal with an angle grinder and 80 grit sanding pad.
While she said it may be possible to repair the boat for use in training, due to internal damage done when she believes the keel hit the ground it can't be used as a racing boat again.
Boat Maintenance; Repair, Tools & Materials; Sails, Rigging & Deck Gear; Standing Rigging; Checking and Replacing: Keelbolts, Part 1 ... It should be pretty obvious that the boat can not be resting on its keel on the ground to this job. The keel must be blocked up, and the supports must be clear of the part of the keel through which the bolts ...
On February 15, shortly after 09:20 YEKT (Yekaterinburg Time), a bright, exploding meteor occurred over the Chelyabinsk oblast. The airburst of the fireball produced a shockwave that hit the city center of Chelyabinsk 1 minute and 24 seconds after the first bright flash and caused considerable damage in and around the city. More than 1,200 people were injured due to broken glass from windows ...
Chelyabinsk Airburst, Damage Assessment, Meteorite Recovery, and ... - AAAS ... c) ) ...
Within the administrative-territorial framework of the Chelyabinsk Region, Kopeysk is a city of regional importance, to which three rural settlements are subordinate.Within the context of local government, it constitutes the Kopeysky Urban District, which, in addition to the city, includes three rural localities: the villages of Kalachevo, Zaozerny and Sineglazovo.
County Clerk offices in Onondaga, Cayuga and Madison counties registered 29 new businesses during the week of Sept. 3 through 6. No businesses were registered on Sept. 2 due to the Labor Day holiday.
General length of all slopes is 7 kilometers. Welcome to Solnechnaya Dolina ski resort to try winter sports even if you are a beginner or professional! The ski resort is located in South Ural, 10 kilometers far from Miass city, 125 kilometers from Chelyabinsk and 250 kilometers from Ekaterinburg. Solnechnaya Dolina is nearby Izvestnaya Mountain ...