ACTIVE STORM TRACKER Hurricane and Tropical Storm Information Learn more
Service Locator
- Angler Endorsement
- Boat Towing Coverage
- Mechanical Breakdown
- Insurance Requirements in Mexico
- Agreed Hull Value
- Actual Cash Value
- Liability Only
- Insurance Payment Options
- Claims Information
- Towing Service Agreement
- Membership Plans
- Boat Show Tickets
- BoatUS Boats For Sale
- Membership Payment Options
- Consumer Affairs
- Boat Documentation Requirements
- Installation Instructions
- Shipping & Handling Information
- Contact Boat Lettering
- End User Agreement
- Frequently Asked Questions
- Vessel Documentation
- BoatUS Foundation
- Government Affairs
- Powercruisers
- Buying & Selling Advice
- Maintenance
- Tow Vehicles
- Make & Create
- Makeovers & Refitting
- Accessories
- Electronics
- Skills, Tips, Tools
- Spring Preparation
- Winterization
- Boaters’ Rights
- Environment & Clean Water
- Boat Safety
- Navigational Hazards
- Personal Safety
- Batteries & Onboard Power
- Motors, Engines, Propulsion
- Books & Movies
- Cockpit Confessions
- Communication & Etiquette
- Contests & Sweepstakes
- Colleges & Tech Schools
- Food, Drink, Entertainment
- New To Boating
- Travel & Destinations
- Watersports
- Anchors & Anchoring
- Boat Handling
- ← Install & Repair
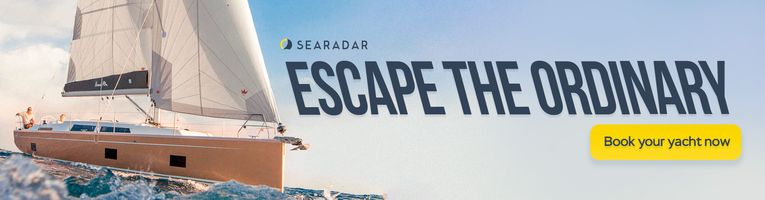
Portlight Replacement
Advertisement
Over time, plastic portlights lose clarity. Polishing can't correct issues like crazing and discoloration. Sometimes pane replacement is the only solution.
Photo: Billy Black
Once you've established that your portlights need replacing, the first thing you need to do is find new ones. If your portlights are round, oval, or rectangular, chances are they're a catalog item originally supplied by a hatch-and-portlight manufacturer such as Beckson, Bomar, Gebo, Lewmar, Taylor, or Vetus. Even irregular portlights are often shared across a number of boat models and become available as off-the-shelf items. If your boat's manufacturer is still in business, their customer-service department can probably tell you who manufactured the original windows. Where an exact match isn't a requirement, locating the appropriate replacement can be as easy as taking a couple of measurements and surfing the Web.
If you find that your particular portlights aren't available as a standard item, the easiest and surely the least expensive option will be to select a standard portlight that requires a slightly larger opening in one or both dimensions. Enlarging an opening is typically just a matter of minor grinding or sawing, while reducing the size of the opening is a major glasswork project. Don't think you can make up the difference with extra sealant.
If you're intent on a perfect fit for an existing opening, and you're unable to locate a suitable catalog-item window, custom manufacture is an option. Check around for small manufacturers in your area or contact one of the big players in this market such as Bomon or Vetus. It's worth noting that many standard-size fixed portlights are also available in an opening version, often at a surprisingly small additional cost. If much of your boating happens in a hot climate, replacing fixed windows with portlights that open will deliver the additional benefit of improved cabin ventilation.
Ins And Outs Of Removal
Old portlights may be screwed, bolted, clamped, or glued in place. Where the flange and/or trim ring exhibits fastener heads (sometimes hidden under a flexible insert), remove these. Anticipate that the fasteners will be corroded in place, so be sure you use the largest available driver that mates perfectly with the fastener. A hand impact tool can be helpful in freeing old marine fasteners. Where the flange is sealed with a gasket, you should be able to separate it from the boat by gently prying with a stiff putty knife, using a second wedge behind to maintain the separation you gain as you work your way around the window. If sealant was used for the installation, you'll likely need to combine cutting with your prying. The best tool is a single-edge razor blade — in a holder initially, then not in a holder to allow deeper penetration. A carpet knife is a good and arguably safer option. The safest way to cut sealant is with leader wire or braided fishing line. Attach dowel handles to a 15-inch length of thin braided wire or line and saw this back and forth in your initial knife cut. Use shallow wedges behind the wire to allow deeper penetration. If, (and hopefully not), the seal is with polyurethane — 3M 5200 — you may need the chemical assistance of DeBond Marine Formula.
Illustrations: Paul Mirto
It's All In The Prep
With the old window out, you'll need to prepare the opening for the replacement. This is also the time to trace a pattern if you're having the replacement custom fabricated. Be aware that there are often substantial differences in port and starboard cutouts on the same boat, so don't assume that a single pattern will suffice for two or more seemingly identical portlights. Trace out and identify a pattern for each opening.
Start your preparation for the new portlight by removing every trace of gasket or sealant material. Scrape with a sharp plastic blade, then buff with a Scotchbrite pad, and finally block-sand with 180-grit paper. If the old sealant was silicone, you have an extra challenge because silicone leaves behind a residue that prevents new sealant, even new silicone, from adhering. With the silicone scraped away, but before sanding, wet contaminated surfaces with a xylene-saturated rag, then blot-wipe clean with paper towels, using lots of fresh paper towels to pick up rather than spread the contamination. Sand only after water misted onto the cleaned surface sheets rather than beads.
Examine the edge of the cutout for damage to a wood core, or to an interior wood liner, and make appropriate repairs. Fill unused fastener holes with a stiff epoxy paste. Don't be surprised to discover that the corner radii are crude or inaccurate. You can improve them with the same epoxy paste. Fair your filled holes and corner adjustments and you should be ready to install the portlights.
Nothing But Pane
Surface-mounted acrylic windows are common on sailboats and can be an economical option for any boat. This is simply a piece of clear acrylic larger than the opening and fastened directly to the cabin side. Overlap all around should be at least an inch, but if the acrylic has a dark tint, its size and shape can be dictated by appearance. No frame is used, but the outside edges of the plastic are typically rounded and polished. Closely spaced fasteners through oversize finishing washers around the perimeter used to make surface-mounted windows unattractive, and prone to cracking, but today's modern adhesives have given surface mounting a fresh lease.
Using black poster board to make patterns will provide a preview of the end appearance. You can have the plastic supplier cut the windows or fabricate them yourself. After appropriate cleaning, de-glossing, and masking or unmasking, the installation process is to apply double-sided VHB (very high bond) acrylic tape 1/2-inch wide by .091 thick (3M 4991) around the entire perimeter 1/2-inch in from the edge, then, taking great care with your alignment — there's no adjusting after the tape touches — press the window to the boat. Mask the pane edge and the boat 1/8-inch beyond the plastic and use a caulking gun to overfill the perimeter gap with Dow Corning 795 architectural-grade silicone sealant. Create a fillet with your fingertip, peel the mask, and your new window is installed.
Easy Install
Your specific installation should be guided by the instructions provided by the supplier of your new windows, so here you're going to find only supplemental guidance. Many modern portlights are sealed by a rubber gasket under the outside flange and clamped in place by screws through the inside flange. If the gasket has a seam, place it at the bottom of the window. The primary concern for gasket-sealed portlights is to make sure the mounting surface is flat. When you dry-fit the window (without the gasket), any gap around the perimeter of the flange must be less than 1/16-inch. You also want the window to slide into the opening without binding. Hole clearance all around of about 1/16-inch is ideal. Paying attention to these two requirements, follow the manufacturer's instruction for installation.
Some manufacturers will instruct you to seat the outside flange onto a bed of marine sealant, either to seal, or to bond, or both. You still need a flat mounting surface and a slip fit. For mechanically fastened portlights, the best bedding choice is butyl tape, a solid sealant that will not be ejected when you compress the flange against the boat.
Portlights to be bonded in place require the adhesive strength of a curing liquid sealant. To avoid squeezing out most of the sealant when you clamp or press the window in place, glue small spacers to the underside of the flange, one at each corner and additional ones as necessary to keep the span between them under 10 inches. Spacers should be 1/8-inch thick and perhaps 1/4-inch across, cut from any plastic or hard rubber and fixed in place with the sealant you're using to bed the flange.
Just before applying the sealant, always wipe both flange and boat with alcohol to remove oily contamination. You'll avoid the potential mess of bad aim if you apply your sealant only to the flange. A suction handle is a useful tool for positioning sealant-coated portlights.
Solid-sealant squeeze-out is easily trimmed away with a plastic blade, but you'll get a neater job with liquid sealant if you first mask both boat and flange edge. Masking the boat 1/8-inch beyond the flange trace line will allow you to shape the sealant into an attractive fillet with your finger (wetted in turpentine for the best effect). This permits removal of the tape before the sealant cures, which avoids problems that occur when the sealant cures to the tape.
If the window clamps in place with internal fasteners, tighten them evenly. Sealant must ooze out the entire perimeter of the portlight, so be sure you apply it liberally. You can wipe away excess, but if you apply too little, you must start all over. The spacers assure a uniform gasket. In addition to your clear view, your boat gets a facelift from this project. That makes it a buy-one-get-one-free deal. No coupon required.
Related Articles
The truth about ceramic coatings for boats.
Our editor investigates the marketing claims of consumer-grade ceramic coatings.
Fine-Tune Your Side Scan Fishfinder
Take your side-scanning fishfinder off auto mode, and you’ll be spotting your prey from afar in no time
DIY Boat Foam Decking
Closed-cell foam flooring helps make boating more comfortable. Here’s how to install it on your vessel
Click to explore related articles
Contributor, BoatUS Magazine
Don Casey has been one of the most consulted experts on boat care and upgrades for 30 years, and is one of the BoatUS Magazine's panel of experts. He and his wife cruise aboard their 30-footer part of the year in the eastern Caribbean. His books include Don Casey's Complete Illustrated Sailboat Maintenance Manual, and the recently updated This Old Boat, the bible for do-it-yourself boaters.
BoatUS Magazine Is A Benefit Of BoatUS Membership
Membership Benefits Include:
Subscription to the print version of BoatUS Magazine
4% back on purchases from West Marine stores or online at WestMarine.com
Discounts on fuel, transient slips, repairs and more at over 1,200 businesses
Deals on cruises, charters, car rentals, hotel stays and more…
All for only $25/year!
We use cookies to enhance your visit to our website and to improve your experience. By continuing to use our website, you’re agreeing to our cookie policy.
JavaScript seems to be disabled in your browser. For the best experience on our site, be sure to turn on Javascript in your browser.
We Ship Worldwide.
- Testimonial
- Create an Account
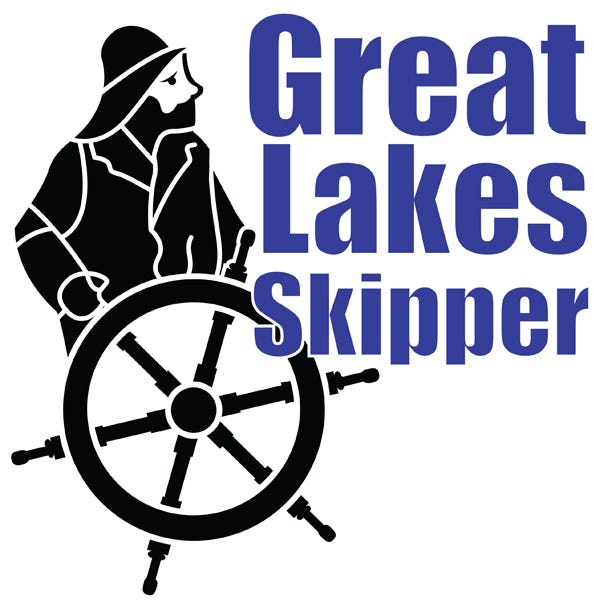
Port Windows and Portlights
Life belowdecks needn't be dim and dismal. Let the sunlight in with new portlights and boat windows from Great Lakes Skipper. Our huge inventory of new and replacement boat parts includes boat windows, fixed portlights, opening portlights, portlights with screens, and marine portlights in a range of colors, shapes, and sizes. We carry boat portlights from Bomar, Gebo, Hi-Tide Manufacturing, Jim Black, Lewmar, Taylor-Made, Diamond Sea Glaze, and many more top brands. Check out our amazing discount prices - you'll love them!
Shop Products
Items 1 - 12 of 119
- You're currently reading page 1

- Privacy Policy
- Terms of Use
- New Sailboats
- Sailboats 21-30ft
- Sailboats 31-35ft
- Sailboats 36-40ft
- Sailboats Over 40ft
- Sailboats Under 21feet
- used_sailboats
- Apps and Computer Programs
- Communications
- Fishfinders
- Handheld Electronics
- Plotters MFDS Rradar
- Wind, Speed & Depth Instruments
- Anchoring Mooring
- Running Rigging
- Sails Canvas
- Standing Rigging
- Diesel Engines
- Off Grid Energy
- Cleaning Waxing
- DIY Projects
- Repair, Tools & Materials
- Spare Parts
- Tools & Gadgets
- Cabin Comfort
- Ventilation
- Footwear Apparel
- Foul Weather Gear
- Mailport & PS Advisor
- Inside Practical Sailor Blog
- Activate My Web Access
- Reset Password
- Customer Service

- Free Newsletter

Blue Jacket 40 Used Boat Review
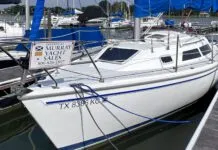
Catalina 270 vs. The Beneteau First 265 Used Boat Match-Up
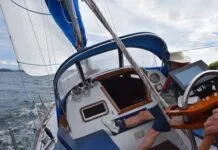
Ericson 41 Used Boat Review
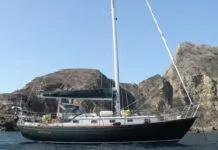
Mason 33 Used Boat Review
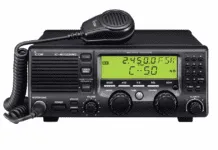
How to Create a Bullet-Proof VHF/SSB Backup
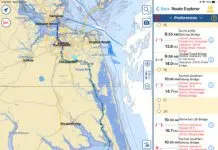
Tips From A First “Sail” on the ICW
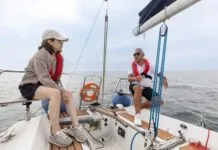
Tillerpilot Tips and Safety Cautions

Best Crimpers and Strippers for Fixing Marine Electrical Connectors
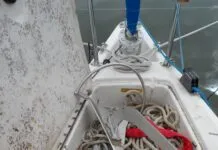
Polyester vs. Nylon Rode
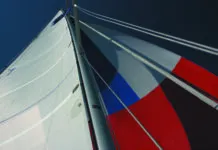
Getting the Most Out of Older Sails
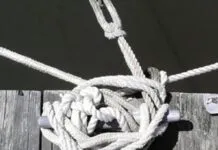
How (Not) to Tie Your Boat to a Dock

Stopping Mainsheet Twist
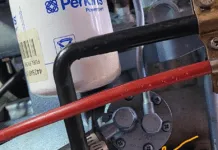
Fuel Lift Pump: Easy DIY Diesel Fuel System Diagnostic and Repair
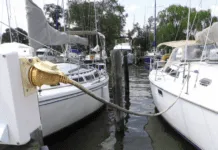
Ensuring Safe Shorepower
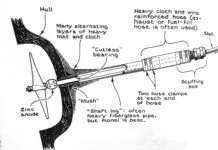
Sinking? Check Your Stuffing Box
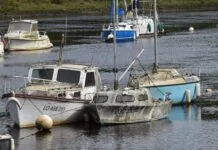
What Do You Do With Old Fiberglass Boats?
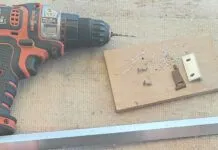
Boat Repairs for the Technically Illiterate
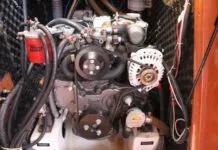
Boat Maintenance for the Technically Illiterate
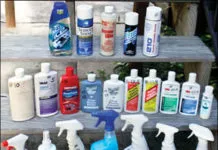
Whats the Best Way to Restore Clear Plastic Windows?
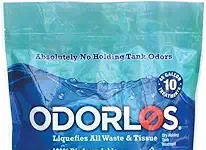
Stopping Holding-tank Odors
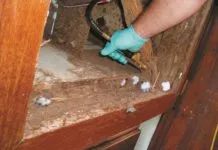
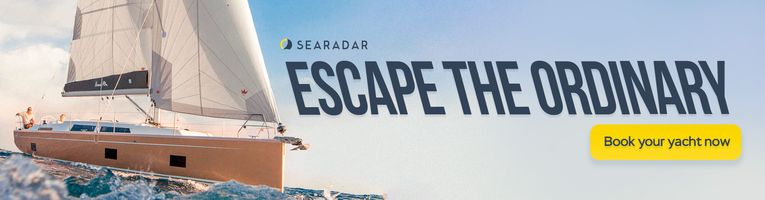
Giving Bugs the Big Goodbye
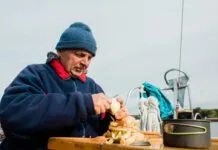
Galley Gadgets for the Cruising Sailor
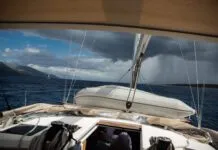
The Rain Catcher’s Guide
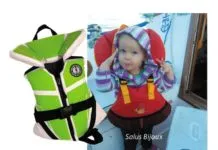
Sailing Gear for Kids
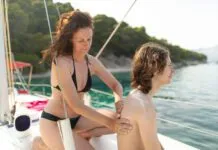
What’s the Best Sunscreen?
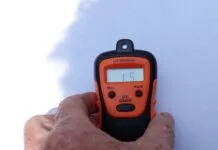
UV Clothing: Is It Worth the Hype?

Preparing Yourself for Solo Sailing
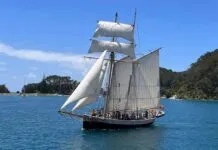
R. Tucker Thompson Tall Ship Youth Voyage

On Watch: This 60-Year-Old Hinckley Pilot 35 is Also a Working…
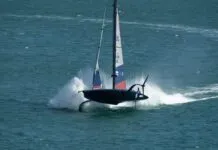
On Watch: America’s Cup
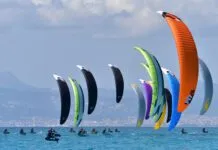
On Watch: All Eyes on Europe Sail Racing
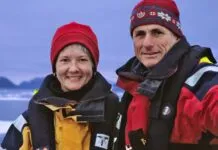
Dear Readers
- Boat Maintenance
F-24 Portlight Replacement

The windows on our Corsair F-24 trimaran were obviously damaged by UV radiation. All we could see through them were shapes of objects that were very close to the windows. That’s what 20 years of exposure does to polycarbonate.
The real motivation to replace them came the day the window seal let go. I was sailing along in a building breeze and heard an odd flapping noise on one side, something like a halyard clanging against the mast, but at deck level. When I went to investigate, I found the front third of the 51-inch portlight was flapping back and forth like a reed, ready to rip off and fly away.
A careful application of duct tape—lots because the deck was wet—secured it for several hours until I reached harbor. There, I dried off the window, reapplied more tape, and planned for a replacement. It was early spring, so it would be months until the weather became warm enough to make a strong installation.

Plastic windows are light, strong and inexpensive. On boats we have two basic choices in glazing material. Acrylic is more UV resistant and lasts many times longer than polycarbonate. Polycarbonate, used in bullet-proof windows, is tougher per square inch, but acrylic is plenty strong—you just need to use thicker glazing in some applications. The chief difference between the two is UV resistance, where acrylic excels.
Eventually, exposure to UV rays damages any plastic, even acrylic, resulting in hazing and crazing within the plastic that no amount of polishing can remove. You can delay this with covers, but after 15-25 years, any clear plastic will likely need to be replaced.
The most common window failure is at the seal. They leak. Leaks can develop over years as sealants begin to fail. The force of thermal expansion accelerates the process. As materials expand and contract with temperature changes, the bond-line between the glazing and the frame is stressed and eventually opens.
In our experience, portlights longer than 30 inches, like those on our F-24 test boat, suffer disproportionately from premature leakage. On our boat, the port side window had begun leaking years before the starboard one let go. Noticing that the previous owner had tried to repair a leak at the forward section of the port window with hardware store silicone, I pumped DOW 795 adhesive sealant into the joint, and this kept the water out.
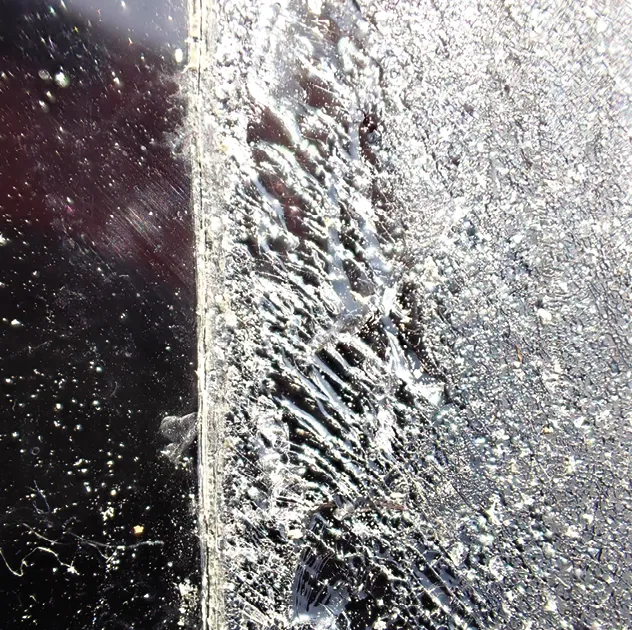
Then the starboard window peeled loose in dramatic fashion, also starting from the forward edge. It was obvious that my too-long windows were expanding and contracting at a rate that was destroying the seal. As a result, I chose to shorten the windows on our F-24 from 51 inches to about half that length.
This had the added benefit of allowing us to cut replacements from a 2’ x 4’ sheet of acrylic instead of a far more expensive 4’ x 8’ sheet. Conveniently, there was an existing column at the midpoint where the two new, smaller windows would join. We got quotes on having the replacements professionally cut to fit, but every quote exceeded $650, so I cut the panes myself. The 2’ x 4’ sheet was only $93; cutting took only a bit over an hour.
WINDOW MATERIALS
Polycarbonate and acrylic are both used for portlights, but not only does acrylic have much better UV resistance, it will remain clear twice as long. Both have similar strength and will not break due to water pressure or foot traffic if made of the proper thickness. However, Lexan has far greater toughness when struck with a hard object (an anchor, for example). This is because it has more elasticity, flexing more before it breaks.
Polycarbonate will block UV but acrylic does not, so we recommend tinting windows to prevent UV damage to the interior (see “ Hatch Tinting Test ,” PS March 2022). UV rays will also attack the sealant. If you need a clear window, polycarbonate might be a good choice, but you have to choose your sealant carefully, since the solvents can cause polycarbonate to craze (see “ The Right Caulk for Your Boat ,” PS December 2021).

CUTTING WINDOWS TO SHAPE
Glazing manufacturers have data sheets describing approved methods for cutting. Polycarbonate is easy to work with, but acrylic is slightly prone to cracking, so we suggest practicing on a piece of scrap first. We have cut rectangular windows using score-and snap plastic cutters. We then carefully round the corners with a sanding disc on an angle grinder. We’ve also cut plastic using a table saw and band saw—using a fine blade and feeding it slowly through the blade.
Perhaps the most user-friendly DIY method for cutting curved windows is using the fine cutting blade on an oscillating multitool. The Fein Multimaster tool was one of the first of this type, but there are many copycats today (see “ What’s in the Practical Sailor Toolbag ,” PS January 2012). Use the old window as a template. Make the cuts using multiple passes and light pressure to avoid melting the plastic. Leave the protective film on during the cutting process. This should remain in place as long as possible to avoid scratching and contamination.
A hole saw is best for larger round holes. Drill small round holes with a twist drill. For drilling acrylic, a sharp tip angle (60-90 degrees) is suggested to prevent grabbing and chipping. Common bits have tip angles of about 120 degrees, which you can carefully sharpen, but better to look for sharp-tip bits meant for cutting soft plastics. Clamping the work helps, as does moderate steady pressure and sometimes a dullish bit. Tight outside curves can be rounded with a sanding disc on an angle grinder, followed by smoothing with fine paper on an orbital sander.
Do not to cut the windows too big. The window must rest flat on VHB tape without touching the surrounding frame. A slight edge bevel (about ½ to 2⁄3 the thickness of the glazing) on the underside of the glazing provides more room for sealant and eliminates a stress riser for the sealant.
There is disagreement on using screws to fasten plastic glazing. Some claim these can lead to cracks in the corners, usually the result of thermal expansion. However, you can prevent cracking by drilling oversized holes. Do not countersink the holes, and when fastening the window, the screws should be snug, but not too tight.
Fasteners offer backup retention in the event of sealant failure. Placed in the corners, they are also convenient for attaching window covers, which protect the new windows from UV, scratches, and bird bombs. We used screws to fasten the windows on our previous test boat, a PDQ catamaran. The seals lasted for more than 20 years, so I was confident we could use them again on the F-24.
If you plan to use screws, pre-drill the glazing before it is bonded into place. You can drill the fastener holes in the frame to line up with these holes later.
INSTALLATION MATERIALS
Our choices of sealing materials are very specific and accepted throughout the industry. As much as I enjoy the search for more economical products, sealing window glazing is not a place to cut corners. The industry standard is to use 3M VHB (very high bonding) tape for sticking the window in place before sealing (see “Through-Bolt Alternatives”). The 5952 family of VHB is best for joining gelcoat to acrylic or polycarbonate. A tape thickness of 1-2 mm is best for providing room for the sealant and allowing thermal expansion.
In addition to the bonding tape, you’ll need a sealant. DOW 795 (DOW 791 in the United Kingdom) is the go-to silicone for structural window glazing. Other silicones do not bond as well, and the window can literally fall out.
Polyurethanes, including 3M 4200 and Sika 295, might seem like a good options, but PS testing and industry experience have found that UV light coming through the glazing eventually attacks the sealant at the bond surface. Many European boats use Sika 295, but they first paint the bond area of the glazing with Sika’s special opaque primer to prevent UV failure.
VHB tape requires an application temperature of 70°F-90°F. It will not bond properly in cool weather, and in very hot weather it will creep. Using space heaters to raise the ambient temperature seldom works. The DOW 795 sealant skims over too quickly in high temperatures and direct sun.
WINDOW REMOVAL
Before removing the old window, tape a tarp to the inside of the cabin. Lots of dirt and pieces of old sealant are going to fall in during the removal and cleaning process. My starboard window was loose and came off with the lightest encouragement from a putty knife. The port window required a much more aggressive approach, but eventually a pair of sharpened drywall knives did the trick. If the sealant is particularly stubborn, try a remover. We found Debond Marine Formula works well for removing all traces of silicone and Re-Mov is excellent for loosening polyurethane (see PS Tests Silicone and Adhesive Removers , PS January 2017). Slit along the bond line with a razor knife as deeply as possible, apply, and let soak for 10 minutes. Repeat.
After 20 years, the original VHB tape will have hardened into a concrete-like material. Neither a scraper or wire brush will be much help. But a heat gun will. The trick is to heat the adhesive enough to soften the tape residue, but not the gel coat. A slightly sharpened 1-inch wide putty knife is the best tool. Round the corners to prevent gouging and to make it easier to work the corners. A nice fat, comfortable wooden handle is best, and wear leather gloves for the heat. It took me four hours with the gun set on high and right in close, not counting breaks. This is the toughest part of the job.
CLEANING UP THE SURFACE
Remove any remaining silicone or polyurethane residue using the appropriate remover (see above) and a small wire brush. You can try solvents, but the removers are many times more effective and will result in less damage to the frame. Clean up the residue with a soapy washcloth, followed by several wipe downs with fresh water. You will also wipe down the surface with denatured alcohol just before applying the primer or VHB tape.
VHB TAPE PRIMER
If the surface is very smooth and non-porous, proceed directly with VHB tape. Old, porous gelcoat should be primed with 3M Tape Primer 94. It dries in less than 15 minutes and provides a slick, impermeable surface that will maximize VHB bonding. Extend the primer under the entire area that the sealant will cover. Do this shortly before applying the tape. Also, if you mask the perimeter of the frame at this time with 3M blue painter’s tape, you won’t have to tape again for the sealant step.
Unless you have used 3M’s primer, wipe the frame one last time with alcohol. Apply a ¾-inch strip of VHB tape around the inside rim of the frame. Trim as needed with a razor blade. Roll the tape firmly into place with its cover strip still in place. A fiberglass laminating roller or wallpaper seam roller works well. It takes several days for VHB tape to reach full strength, but after 20 minutes it will achieve a good bond.
Once the VHB tape touches the glazing it will grab the glazing. The window can’t be repositioned, and there are no second chances. Dry fit the glazing with the tape’s protective cover still in place. Place spacers around the perimeter of the frame to ensure perfect fit. These will help guide the window into a centered location. Short pieces of ¾ x 1/8-inch aluminum angle work well. We’ve also used popsicle sticks. You can tape your spacers in place if needed. The window may require trimming so that it sits flat on the VHB tape. An angle grinder with a 150-grit wheel works well for small adjustments.
Remove the red release strip from the VHB tape. Remove the inner protective film from the glazing and wipe the bonding edge with alcohol. For larger windows, you’ll want two people for fitting. Place one corner first, and then ease the window into place. Once in position, press firmly all around the perimeter several times, as you did for the tape. You don’t need a roller; palm pressure is sufficient.
Screws are optional. If you are installing screws for cover snaps or for retention, this is the time to drill the holes into the frame area. You could drill these holes later, but then the chips from the drill will land in the wet sealant. Drill either for #8 machine screws or #8 self-tapping screws.
Remove the spacers and mask the perimeter of the frame and glazing with 3M blue painter’s tape. (You should have already done this during the taping process.) Leave the outer protective film on the glazing and you will not need to mask it. Use a high-ratio caulking gun like the 26:1 JES M26S for better control (see “ Caulking Gun Shootout ,” PS August 2021). Pump the DOW 795 (DOW 791 in the UK) into the gap, filling the space from the VHB tape out to the surface. A 3/16-inch hole in the pump spout is about right. Wipe off any excess sealant and allow it to set for about 5-10 minutes. Do not continue wiping after the first pass; the sealant skins over rather quickly in warm weather, and any smoothing attempts now will just make it look worse. Avoid working in direct sun if possible, or at least avoid the middle of the day for this critical step.
Peel off the masking tape and protective film very carefully, before the sealant has skinned over. Do not allow the sealant to dry before peeling the tape.
Install the screws. No more than finger tight to avoid stressing the plastic. A cone of sealant under the head prevents leaks.
With care, your new windows should provide another twenty years of trouble-free service.
3M, www.3M.com
FEIN, www.fein.com
PLEXIGLAS, www.plexiglas.de
SABIC (LEXAN), www.sabic.com
SIKA, www.sika.com
SUNBRELLA, www.sunbrella.com
YKK, www.ykkfastening.com
F iberglass and plastic windows expand and contract at different rates. As the temperature swings from 20 ° F to 110 ° F in the sun, a window that is 1 meter long can theoretically expand in length by 1.5 mm. The materials used for installation (VHB tape and silicone) allow for that much movement, but it’s not good for them in the long run.
Of course, the actual movement is far less. If the window moves equally in all directions, that reduces the total distance by 50 percent. With any luck, you installed the window on 75 ° F day, reducing the maximum temperature swing to about 50 ° F. This reduces expansion to about 0.5 mm, still enough to strain any seal.
Shorter windows will expand less, so if you have windows that are more than 36 inches long, our advice is to limit them to 30 inches (0.76 meters). This reduces expansion to 0.38 mm or 0.015 inches (about 1/64-inch).
As a practical matter, what does this mean? Use the thicker 1⁄8-inch VHB tape for bonding the window in place; it adapts better to rough surfaces and has a greater range of motion. Make sure your beads of sealant are at least 1⁄8-inch wide. Beads that are 3 ⁄16-inch are better; the glazing should not be a tight fit in the opening. Drill oversized holes for any fasteners; ¼-inch is about right for #8 screws.

1. Our installation left plenty of room for thermal expansion at the corners. Getting a smooth finish on the DOW 795 is tricky. It helps to practice first.
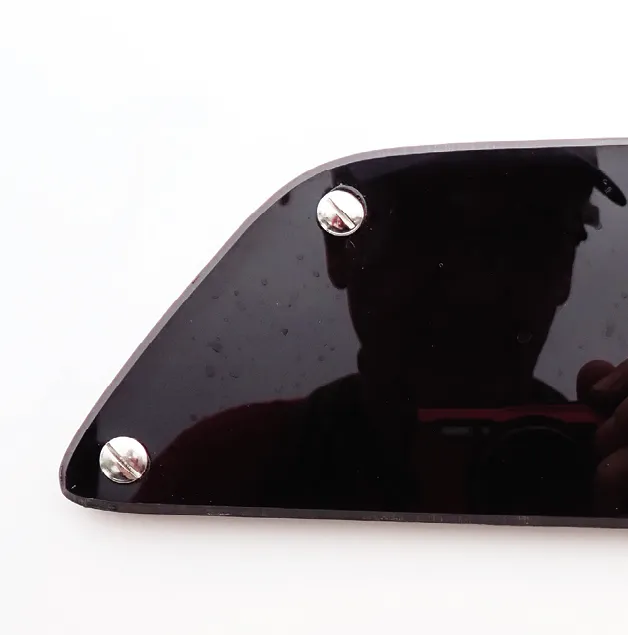
2. We drilled oversized holes in the glazing so that the screws would not cause stress cracks.
B efore using 3M Very High Bond (VHB) tape to bond our acrylic windows in place, we had to remove the old tape. A scraper and a heat gun helped remove the old tape. Once the surface was clean and free of all tape residue, we applied 3 M Tape Primer 94 to ensure a good bond.

1. Keep the heat gun moving so as not to overheat the gelcoat.
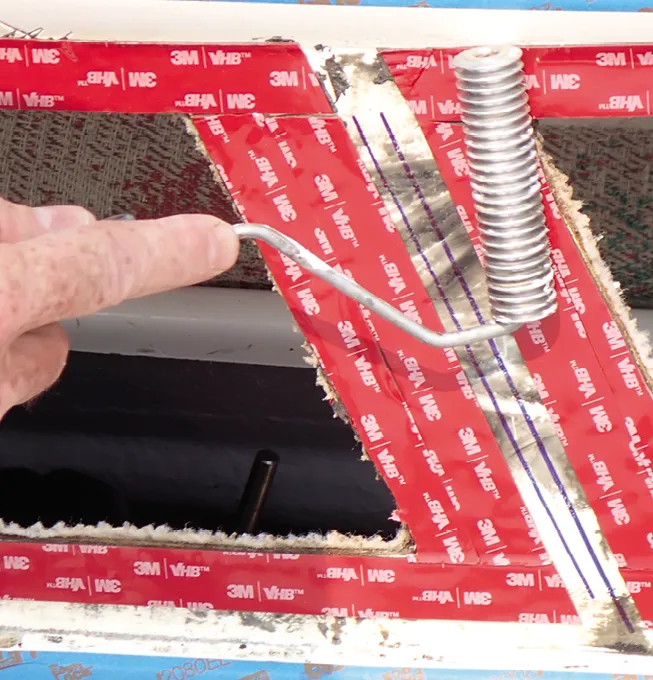
2. We used a grooved laminating roller to firmly press down the tape and ensure a good bond.
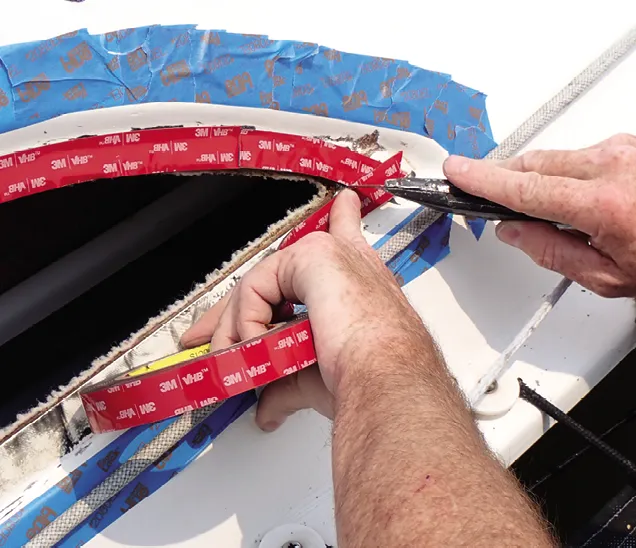
3. A sharp box cutter was used to trim the tape to fit.
I f you like sewing, making your own window covers will be a cakewalk. But for those who aren’t adept at machine-stitching, you can create your own durable cover by gluing on a reinforced “hem.”
Cut the covers to size, adding about ¼-inch for every foot in length to allow for shrinkage. Also add about ½-inch all around to allow for trimming after you’ve glued on your reinforcing “hem” of material. Cut strips of 1½-inch wide canvas to match the length of each side of the cover, adding about 1-inch length in each strip for overlapping at the corners. This will be your hem.
Run a generous bead of sealant down each side on the inside of the cover. If possible, pick a sealant color that matches your cover. Because you will be trimming the hem and cover, the sealant should run about ½-inch inside the true size of the cover, or about 1-inch inside the pre-cut cover. Press the strips into the bead, plus a dab of sealant between them where they overlap in the corners. Roll the strips down firmly (a laminating roller works well), squeezing sealant across the full width of the strips. Allow to cure.
Use sharp scissors to trim the covers to size. The laminated canvas will now have a consistency something like the sidewall of a bicycle tire. It will not fray. There will be double layers of cloth down each side and three layers in each corner, creating a very strong location for the corner snaps. Punch the required holes for the snaps and install the snaps in the corners.
If your windows don’t have snaps and you don’t want to retrofit them with screw-in snaps, you can use self-adhesive snaps. YKK makes the best ones, under the name SNADs (SNap ADhesive mounted). Install the self-adhesive snaps about 1 to 2 inches outside the widow frame. They are available in both all-plastic and metal insert versions. They are mounted with 3M VHB tape, so if you take the same surface preparation and installation precautions you did for the window, they should be permanent. Cost is about $4 each.

1. Keeping the cover loose reduces strain on the snaps.

2. We put snaps at every corner and spaced them evenly along the sides, top and bottom. Not every screw was a snap.

3. Adhesive snaps like the YKK SNADs make it easy to retrofit windows with a snap-on cover.
RELATED ARTICLES MORE FROM AUTHOR
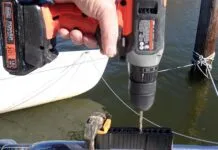
Mastering Precision Drilling: How to Use Drill Guides
Leave a reply cancel reply.
Log in to leave a comment
Latest Videos
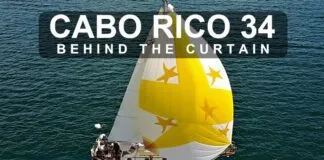
Cabo Rico 34 Boat Review
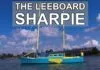
Super Shallow Draft Sailboat: The Leeboard Sharpie
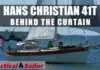
Hans Christian 41T – Boat Review
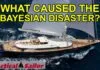
Seven dead after superyacht sinks off Sicily. Was the crew at...
Latest sailboat review.
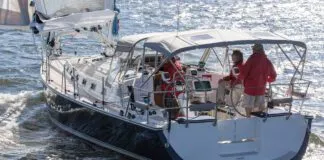
- Privacy Policy
- Do Not Sell My Personal Information
- Online Account Activation
- Privacy Manager

My Sailing Fix

Portlight Replacement
The opening portlights on Priorities began leaking when the boat was about 18 years old. The rubber seals had cracked over time and were no longer effective, especially due to the sheer of the sides of the cabinhouse. Actually, the four portlights in the main cabin had been replaced by a previous owner, so problems may have began before I even bought her.
The forward head leaked especially bad, making its shade mildewy, though it at least dribbled into the sink. The aft head portlight caused rainwater to puddle under the toilet, initially leaving a “Uh, what is the puddle of mystery liquid appearing under the hoses of the toilet?” reaction when I first noticed it occurring.
Priorities is a Catalina 400, hull number 53, informally referred to as a “Mark I” after the updated “Mark II” was released in the late 90s. Much (or maybe all) of the Mark Is were equipped with Lewmar “Old” Standard Portlights… 6 opening size 2s forward, 2 opening size 0s aft, and four fixed portlights below the toerail (I think sizes 2 and 0).

Lewmar changed the design of their “Standard” Portlights in 1997 but kept the name “Standard,” so the two versions are now referred to as “Old” Standard and “New” Standard. The cutout dimensions are almost but not exactly the same, though after replacing 4 portlights on Priorities I haven’t needed to make any modifications to the cutouts in my hull for any portlight. New Standard portlights have an upgraded dogging (or latching) system, where the dogs are pressed to lock rather than twisted to lock. There’s also only one joint in the outer frame rather than two, which probably makes it stronger and therefore more likely to seal.
Replacing the seals in the Old Standard Portlights was something I considered since it didn’t require removing the entire assembly. A new seal and new dogs on each portlight were around half the cost of a new portlight, but still left me with old windows that were starting to craze. Researching online also made me wary of the probability of success I might have when replacing the seals, and I learned it might take quite a bit of time.
My lack of confidence in repairing the portlights led me to replace them instead. Since the new ones were nearly a drop-in replacement, I figured it wouldn’t take much longer (and might be faster) to replace rather than repair, and I’d have a better design with new windows.
Removing the inner plastic trim piece on each portlight was easy since they merely snap on and off. After the trim was removed, the hull cutout was easily visible and measureable, revealing my first challenge: the hull cutout thickness (40-50mm) was slightly more than recommended in the installation instructions. This was somewhat of an issue since the included stainless steel metric screws used to attach each portlight were too short, and replacements of the proper length weren’t easily available at the local hardware stores. The screws couldn’t be too long, either, because they can’t contact the outer flange of the frame without stripping the inner flange screw holes. Additionally, the plastic trim might not quite be long enough.
Measuring the screws used to attach the old portlights, which didn’t seem to use metric threads, led me to order a bunch of 40, 45, and 50mm screws from McMaster-Carr . Since McMaster ships from several locations in the US, including Chicago, I received them within 48 hours of my order.
I removed and replaced each portlight before moving to the next portlight so if I encountered obstacles along the way I wouldn’t have too many holes in the boat. Since there’s no cure time with my chosen bedding sealant, I could replace one portlight in the morning, then go for a sail in the afternoon, spreading the project over a few days (some I did in the boatyard).
Prior to removing each portlight, I test fit each new portlight over the old to see how reasonable the fit would be… the New Standard Portlights have a slightly different curve in each corner than the Old Standard, though it was always a good fit on Priorities.
Removing the old portlights were really the only other minor challenge. Catalina installed them with a sealant that has some adhesive properties (maybe 3M 4200), so I had to carefully use a hammer and putty knife to break the seal after removing the screws. Each portlight took 30-45 minutes to remove because of this.

In preparation for the new portlight, I spent a little time making sure the gelcoat around the opening was clean and smooth. It doesn’t need to be perfect, but removing silicone or other old caulk is important for getting a good, watertight seal when using any bedding compound.
As a sealant, or bedding, for the new portlights I used Bed It Butyl Tape by Compass Marine . Compass Marine is owned by Practical Sailor contributor Rod Collins, who also regularly contributes his expert advice as “MaineSail” on various boating web forums like Sailboat Owners.com . I’ve used his butyl tape for bedding lots of deck hardware and it’s been excellent… it works very similar to plumber’s putty, but in tape form and a little bit stickier.

After carefully squishing each new portlight in place, I gradually tightened the mounting screws in back. I tightened in a sequence similar to tightening a cylinder head, working my way from screws in the center and out to screws in the sides of the frame. Since there’s only about 7 or 8mm of space between the inner and outer flanges of the frame, and the screws can strip if they are screwed in too deeply, I would start with using screws that were just barely long enough to get a few threads in the frame. After a few rounds of gradually tightening each of the 12-16 screws, which also squished the bedding compound, I would replace some of the screws with slightly shorter screws one by one, thus allowing me to gently bring the screws to final torque without hitting the other flange of the outer frame. Final torque should only be 25 in-lb., which isn’t super tight.

Approaching final torque, I tested the operation of the portlight by opening and closing it a few times. The new portlights are built so solidly I never really got worried about it binding when opening or closing.

A cool thing about using butyl tape is that it never cures or dries. However, it does slowly “ooze,” so a day after installation I retightened the screws to final torque, then carefully trimmed the excess butyl tape away. When trimming the butyl tape, it’s important NOT to pull any more material out from under the frame… I used a sharp knife to cut the excess.

I tested watertightness with a hose, as well as after several rainstorms, and never had any issues.
After testing for watertightness, I installed the new trim piece. The plastic trim simply snaps in place on the inner frame after trimming its depth to fit. Since all of my portlights were in thick parts of the hull, mine required no trimming at all. A small, nearly invisible space exists between the trim and the inner flange of the outer frame, and I may fill that gap with a white tape to prevent water from getting trapped between the trim and the hull… if I ever get around to it.

In the end, each portlight took about two and a half hours from start to finish, not including time to measure or read the instructions. It actually was pretty easy, too, and now we have clean, leak free, opening portlights in both our heads!

Share this:
- Click to share on Twitter (Opens in new window)
- Click to share on Facebook (Opens in new window)
One thought on “Portlight Replacement”
Old standard and new standard portlights require the same length and width cutout dimensions. The variance is the corner radius. Old standard uses 58mm versus 62mm for the New standard meaning the OS cutout is more squared off. That means at its largest in the middle of the corners the OS cutout with be about 3.5 mm larger than the NS. If the original cutouts on your boat are precise without much slop, the NS will work in the corners, but without a lot of outer frame bearing surface to spare. Dry fitting a NS portlight into your existing cutout will tell you where you stand. I too like Bed-It butyl elastomer hybrid tape for this application, with a couple caveats. Bed-It tape is 1.58 mm thick so you might want to start with a little more than 1 layer. When clamping inner and outer frames together compress enough to achieve squeeze out slowly over multiple tightening events and multiple days. To avoid failure do not compress the butyl to less than 1mm. When squeeze out is complete check mounting screws periodically to make sure they stay snug. Bed-it is not an adhesive, and I was surprised to find many of the screws I was removing were loose. Lewmar offers a torque spec for the mounting screws of 25 in lbs in the instructions, you may have to balance that against excessive squeeze out. Note the included screws from Lewmar are pozidriv, not Philips, and require a PZ2 bit, otherwise you risk cam out of the screw head.
Leave a Reply Cancel reply

Please verify you are a human
Access to this page has been denied because we believe you are using automation tools to browse the website.
This may happen as a result of the following:
- Javascript is disabled or blocked by an extension (ad blockers for example)
- Your browser does not support cookies
Please make sure that Javascript and cookies are enabled on your browser and that you are not blocking them from loading.
Reference ID: 0868fd0e-70ee-11ef-93d7-40cb247a6229
Powered by PerimeterX , Inc.

- Forums New posts Unanswered threads Register Top Posts Email
- What's new New posts New Posts (legacy) Latest activity New media
- Media New media New comments
- Boat Info Downloads Weekly Quiz Topic FAQ 10000boatnames.com
- Classifieds Sell Your Boat Used Gear for Sale
- Parts General Marine Parts Hunter Beneteau Catalina MacGregor Oday
- Help Terms of Use Monday Mail Subscribe Monday Mail Unsubscribe
Rebedding fixed portlights
- Thread starter PrincessoftheLake
- Start date Apr 17, 2010
- Hunter Owner Forums

PrincessoftheLake
Today I removed both of the large fixed portlights on port and stbrd of our 1995 Hunter 40.5. I have scraped the fiberglass clean and have started work on the plexiglass. My question is what is the best way to completely remove all the sealant from the plexiglass without scratching it?

PrincessoftheLake said: Today I removed both of the large fixed portlights on port and stbrd of our 1995 Hunter 40.5. I have scraped the fiberglass clean and have started work on the plexiglass. My question is what is the best way to completely remove all the sealant from the plexiglass without scratching it? Click to expand
Thanks, Maine Sail. After trying to clean the plexiglass yesterday the Skipper and I decided that we are just going to replace the plexiglass since they are both pretty crazed. You mention Dow 795 as the product to use. Where do you find it? Thanks, POTL
Jetpilotbob
Two products you can try depending on how badly glazed your plex is; first, 3M makes a fiberglas polish/restorer that I think comes in a white/green or white/blue bottle and can be purchased at any West Marine. Works pretty good magic. Use it on friends' cars all time to restore their glazed/crazed headlight covers. Second, an aviation product called "Micro Mesh" is a multi-step product and something of a pain to use. Can obtain it from most pilot shops or Sporty's Pilot Shop. Try the 3M product first, tho.
PrincessoftheLake said: You mention Dow 795 as the product to use. Where do you find it? Thanks, POTL Click to expand
Thnaks Maine Sail. I did try the 3M product on the plexiglass last year and while there was some improvement it was not much. I appreicate the link about the Dow product. Thank you.
Replaced the milk-white skylights on my Legend 37 with 3/8" Bronze Lexan last fall. I used Dow 995, but only sealed around the edges of the new lenses, since the Lexan needs to be able to expand and contract. I purchased the 995 from ebay, but don't recall the seller. The cost of a tube was about $15.
That's a good idea. The old portlights that I took off were sealed around the edges and sealed to the hull in the middle of the two portlight openings. Based on your comment perhaps I might dispense with that step. It does make sense to me.
Hunter Re-bed Hunter has a bunch of sailboats with fixed sky lites, Just finished re-bedding my four lexan set ins. I used Dow Coning 732 as the sealer. This 732 is a new product that is superior to the 79X family for one reason. Shelf life. My tube of DC 732 does not expire until May of 2012. The DC family of 79X sealant would only last about 4 to 5 months if you were lucky to get a new tube. Broad Reach
Re: Hunter Re-bed The recommendations seems to be for the DOW product but I am wondering if there is any reason to not use LifeSeal product? Any thoughts on that?
PrincessoftheLake said: The recommendations seems to be for the DOW product but I am wondering if there is any reason to not use LifeSeal product? Any thoughts on that? Click to expand
Tony D'andrea said: I hear the question as to which sealant to use when bonding Acrylic, or Polycarbonate to aluminum, stainless or FRP over and over and over..... Well here goes... The only three adhesives I would consider using are Sika Flex 295 UV with the primer, GE SG-4000, and Dow 795. Using the correct adhesive is only 1/2 the battle. Do not apply the sealants below 50 degrees F. The temperature must maintain at least 50F during the entire 21 day cure cycle. Cut this corner and your finished before you start. Preparation of the bond area is also very/ very important. DO NOT TOUCH THE BOND AREA WITH YOUR BARE HANDS! Contamination from the dirt and skin oils will make a solid cure impossible. You may clean the FRP and metal with acetone to prep the area but if you touch the Lexan or Plexi with harsh solvents you will ruin the portlight. A 50/50 mix of isopropal alcohol and distilled water will work well to clean the plastic if needed. Remember that clean enough is not clean enough. Click to expand
Tony D'andrea said: Acrylic -vs- Polycarbonate Consider the Following: All major hatch, portlight and window manufacturers use Acrylic in offshore / bluewater marine products. Acrylic is more scratch resistant than standard (9034) polycarbonate. Acrylic is significantly more durable when exposed to Ultra Violet radiation (sunlight). Acrylic is less expensive than Polycarbonate. Don't misunderstand my preference for acrylic. I buy, use and sell a significant amount of both products and each has its application. In my humble opinion Acrylic is more durable, versatile and cost effective in the hands of a skilled craftsman than polycarbonate. Additional considerations may include polycarbonate with UV and scratch resistant coatings. While these products are heavily promoted by several manufacturers and carry 5, 10 even 15 year warranties the following information has been reported in "real life"applications: Polycarbonate is impact resistant. When its new it is almost impossible to break. Small quantities (less than a 4 by 8) in gauges over 1/8th inch are difficult to to find in the uv/scratch resistant grades. Colors are limited. Only two standards (gray and bronze). Try and find anything thicker than 1/4 in UV/ scratch resistant! Polycarbonate foreshortens when subject to static or dynamic loads. What this means is if you replace your hatch lens with polycarb, seal it and then step on it the ductile material will deflect (bow) in the center. One of two things may happen. 1st you will surely break the watertight seal, 2nd you may end up with a leg in your galley. As for the warranty: The original owner is warranted against failure subject to the material being submitted to the distributor for evaluation with the original invoice subject to actual replacement cost at the time of purchase. I guess this means they sell you a new square of material and apply the old payment to the new cost. How about the labor to fabricate the part, install it and sealant? Why take the chance? Polycarbonate is a great material, The US Air force uses it for fighter canopies! I sell Polycarb to the USCG and US Navy. Remember they don't mind using it because we are paying to replace it every three years. Both Acrylic and Polycarbonate have specific uses and installation requirements. Cast Acrylic (of a specific thickness) is in accordance with CE and ABYC guidelines, and installed on virtually all of the big blue water sail boats produced on both sides of the pond. Polycarbonate is commonly used as a replacement due to its ease of fabrication and incredible initial strength. The USCG and USN require Polycarbonate on their vessels but they also have a PM cycle of 36 to 42 months for change out. My Tax dollars at work... Due to its ductility Polycarbonate it is more challenging to install. I have seen Sika Flex 295UV with primer and Dow 795 both mentioned. I use and recommend both. Don't go over 4 ft continuous length with a fixed portlight. Remember the coefficient of thermal expansion for Acrylic and Polycarbonate is in the neighborhood of .000039 per inch per degree F. That means an 8ft plastic port will expand and contract up to 1/2 of an inch from the coldest day in Feb to the hottest day in summer. WOW!! Compartmentalize the job. It will be easier to install and less prone to leaks. Never ever bolt a plastic portlight in place. Screws are fine to hold a lens till the adhesive cures. Take them out asap and fill the holes with the aforementioned products. Both of these products are rated at 700 + percent elongation before tear. Strong flexible and UV resistant. Kinda like me! Been to a boat show lately? Seen any screws? Glass is good so long as your boat does not twist or torque. Show me a fiberglass boat that does not twist and I will show you a cocktail barge tied to the dock. Click to expand
I would be interested in hearing how the replacement goes. Can you also share where you end up getting the portlights fabricated and what material you end up using. Sounds like Select Plastics makes a strong case for acrylic. Mine are crazed too and I would like to replace them at some point.

The ports have been out off the boat for several years. I had planned on painting the deck with two part paint before rebedding new ports. Is that a good plan or would I be better off installing the ports first?

If you follow the following link to the Dow web site and enter the state that you reside in they will indicate the places were 795 can be purchased; http://www.dowcorning.com/applicati...01595717&prod_ids=PROD&country=USA&language=E . Also, as Main Sail has mentioned the spacers are very important.
My husband found a place in Minneapolis that did the portlights. Each piece is over 5 ft long and we had them done in 5/16 acrylic. The guy that did them did a great job on the beveled edge. We compared and they were identical to the old ones in size and shape. The install of the new went well. The hull surface had been scraped and sanded clean. I wiped the fiberglass down with acetone before applying the sealant. As suggested we used the Dow Corning 795. Great stuff. We put the windows in place, shimmed them up and they never moved. Captain Grumpy taped them snugly in place and then we tarped over them and left them to cure until we go up the week after next. I will finish off the seal on the outside edge then. I can't wait to see how nice the new windows look!

Marco Garcia
Hello Princess, Would you mind sharing how much for the Acrylic portlights?? I wonder if he kept a mold for your fellow 40.5ers? Same color? Thank you..

Marco Garcia said: Hello Princess, Would you mind sharing how much for the Acrylic portlights?? I wonder if he kept a mold for your fellow 40.5ers? Same color? Thank you.. Click to expand
Marco- For the two pieces we had cut it was $350 with tax. The color is just a little lighter than the original and just a tad thicker.
Thank you Princess, Let me know when you go sailing how they work out, perhaps I'll get a couple of them for my end of the year proyects...

We may have to do this soon for our 1996 280. While thinking through the reinstallation process; what technique did you guys use to initially guide the "window" into position and what thickness of shims are required for the sealant . . . 1/16, 1/8, 3/16??
- This site uses cookies to help personalise content, tailor your experience and to keep you logged in if you register. By continuing to use this site, you are consenting to our use of cookies. Accept Learn more…
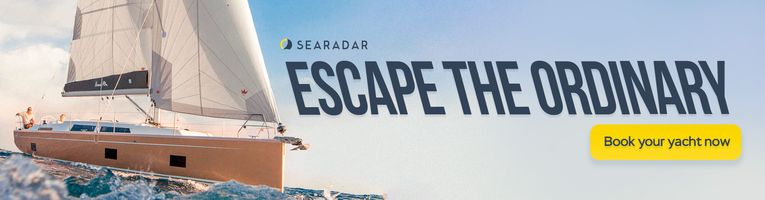
IMAGES
VIDEO
COMMENTS
For longevity the hands-down winner is tempered glass—the 40-year-old opening ports on our boat are as clear as the day they were installed—but because glass is brittle it should only be installed in a rigid frame. That generally rules it out for fixed portlights, even those with metal frames, because such frames are not rigid, but flex to ...
Round Fixed Portlights. Available in 2 options. $545.05 - $757.89. In Stock. Man Ship Marine SS Rectangular Opening Portlights - Angled Spigot. SKU: 1002595 | Item ID: MNS LS-0512-15A. ... Opening Portlights: Ideal for ventilation, these boat portlights can be easily opened and closed. Parts & Accessories: ...
Discounts on fuel, transient slips, repairs and more at over 1,200 businesses. Deals on cruises, charters, car rentals, hotel stays and more…. All for only $25/year! Over time, plastic portlights lose clarity. Polishing can't correct issues like crazing and discoloration. Sometimes pane replacement is the only solution.
Our huge inventory of new and replacement boat parts includes boat windows, fixed portlights, opening portlights, portlights with screens, and marine portlights in a range of colors, shapes, and sizes. We carry boat portlights from Bomar, Gebo, Hi-Tide Manufacturing, Jim Black, Lewmar, Taylor-Made, Diamond Sea Glaze, and many more top brands.
515. Catalina C25 3559 Rocky Mount. Aug 11, 2020. #1. I am replacing my leaky, deteriorated windows on my 1984 Laguna 26. The original windows seem to be obsolete, so I am looking at .25" cast acrylic and cutting them .75" oversize all the way around and bonding them in. As an autobody man, my first thought was windshield urethane, but it is ...
In our experience, portlights longer than 30 inches, like those on our F-24 test boat, suffer disproportionately from premature leakage. ... (see "The Right Caulk for Your Boat," PS December 2021). Fixed in place on top of our patterns, the acrylic panels were fairly easy to cut using an oscillating multitool.
1 Many years ago, a previous owner had replaced the fixed ports on this 1973 boat with homemade surface-mounted acrylic sheet. Now they were so clouded you couldn't see out. 1A. Step one was to make templates of the portlights. I traced the outlines of the insides of the cutouts onto paper and sent them off to Vetus.
Installing the new ports was a straightforward task. Each came with an exterior trim ring, a split interior trim ring, a roll of adhesive gasket and a set of fasteners sized to the wall thickness of the cabin side. I dry-fitted each one several times, marking for the right opening and top and bottom. After that, I applied the gasket material to ...
Thanks for watching!Consider supporting on https://www.patreon.com/sailbrosFollow us on Instagram: http://instagram.com/sailbros/Like us on Facebook: https:/...
Hunter 37.5 Santa Barbara CA. Jan 5, 2016. #8. I replaced the 4 long fixed portlights on my 1993 Hunter 375 with 1/4" thick plexiglass. Getting the old ones out was (alarmingly) easy... after removing the interor trim, push hard from the inside. On the 375 they are not screwed or mechanically held in place.
Strangely enough, after 24 years of exposure, the forward fixed hatchlight looks brand new. Not a blemish and crystal clear. The side fixed portlights however, have varying amounts of damage from UV over the 24 year. This one looks like the product of a drive-by shooting :
The opening portlights on Priorities began leaking when the boat was about 18 years old. The rubber seals had cracked over time and were no longer effective, especially due to the sheer of the sides of the cabinhouse. ... and four fixed portlights below the toerail (I think sizes 2 and 0). Original Lewmar Old Standard Portlight in forward cabin.
Step#1: Make a Template. The first thing you need to do is to make a template of your portlight. This will help you determine what size portlights you need for your boat. In this case, you need to trace the outline. Make sure to trace the porthole from the inside of your boat. For this purpose, you can use any paper that is easy to handle while ...
3. Beneteau 350 Washington, NC. Mar 16, 2018. #1. The fixed windows across the cabin of my '87 Oceanis 350 are past the point of repair. We rebedded them 2 years ago, but they are now badly crazed, leaking again, and the starboard curved window has a crack. This boat was built in France and word is that the molds are long gone.
Lewmar's comprehensive range of hatches and portlights offers a solution, whether on a small day boat or superyacht. Combining years of manufacturing experience with the latest in design trends, the Hatch and Portlight Range bears all the features you have come to expect of a high-quality Lewmar product. Hatch & Portlight Guides.
4317A S Sheridan Rd , Tulsa OK 74145-1120. home. categories. plumbing & ventilation. marine ventilation. boat hatches & portlights. Check your spelling or try fewer, more generic words. If you're really stuck, visit the. Replacement Gas Struts for Dock Boxes & Hatches, Fits 10mm Ball Stud Unless Noted Otherwise.
Case Study: Installing custom-made Vetus portlights on a 1970s cruiser. 1. Many years ago, a previous owner had replaced the fixed ports on this 1973 boat with homemade surface-mounted acrylic sheet. Now they were so clouded you couldn't see out. 1a. Step one was to make templates of the portlights.
Upgrade your boat with Beckson portlights or opening ports. Shop high-quality Beckson ports, marine portlights, and portlight parts for superior durability. Need Help? ... Round Fixed Ports - Plastic. Available in 5 options. $32.61 - $69.95. In Stock. Beckson Portlight Cam Latches . SKU: 92372 | Item ID: BEC PRK-W312.
Continuing in my quest to rid the boat of leaks, I've been getting a good amount of water coming in through one of the fixed portlights on my 03 356. It's the starboard side portlight, aft of the bulkhead. I have water coming in from under the frame, as well as running down the liner and onto the top of the galley cabinets.
Shop our selection of high quality Man Ship Stainless Portlights and Accessories perfect for any boat! Skip to Content. Home; Blog; Check Order Status; Shop By Parts Brands; FAQs; Resources; Returns; Call Us: 855.215.4211. Intl: 909.393.0016 ... Portlights listed below are in stock and ready to ship. If you would like a different or custom size
If you do not receive an email contact Customer Service. 1400 NW 45th Street , Seattle WA 98107. Home. / Categories. / Plumbing & Ventilation. / Marine Ventilation. / Boat Hatches & Portlights. / Portlights.
Hunter has a bunch of sailboats with fixed sky lites, Just finished re-bedding my four lexan set ins. I used Dow Coning 732 as the sealer. This 732 is a new product that is superior to the 79X family for one reason. Shelf life. My tube of DC 732 does not expire until May of 2012.